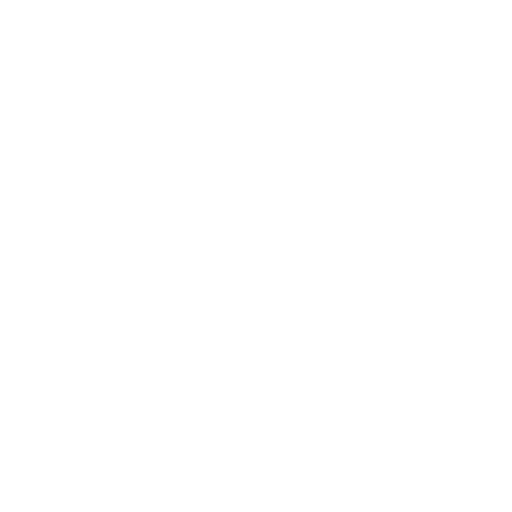

Stress vs Strain: Formula, Relationship & Real-Life Examples
Stress and strain are two key concepts that describe how materials respond to external forces. These ideas help predict whether an object will bend, stretch, or break when a force is applied. Understanding the difference between stress and strain is fundamental in mechanics and materials science, especially when analyzing solid objects and structures.
What Is Stress?
Stress is defined as the force per unit area that acts within a material. When external forces are applied to an object, stress measures how much internal force develops inside the object in response to those external influences. The most common symbol for stress is σ (sigma).
Several types of stress may occur, including:
- Tensile Stress (σt): Force that pulls or stretches the material.
- Compressive Stress (σc): Force that compresses, pushes, or shortens the material.
- Shear Stress (τ): Force that acts parallel to the surface, causing sliding between layers.
Stress is measured in pascals (Pa) or newtons per square meter (N/m²). The formula to calculate normal stress is:
where F is the applied force and A is the cross-sectional area. Stress analysis is vital in engineering for assessing material safety and behavior under different load conditions.
What Is Strain?
Strain measures the deformation that a material undergoes when subjected to stress. It describes the fractional change in an object’s dimension due to the applied force and does not have any units (it is dimensionless).
The basic strain (ε) formula for a change in length can be given as:
where ΔL is the change in length and L0 is the original length. Types of strain correspond to types of stress:
- Tensile Strain: Occurs due to stretching.
- Compressive Strain: Produced by compression or shortening.
- Shear Strain: Results from sliding action between layers.
- Volumetric Strain: Change in volume relative to original volume.
- Thermal Strain: Caused by temperature changes.
Strain is measured as a ratio or as a percentage, indicating how much a material deforms under load relative to its original size.
Key Differences Between Stress and Strain
Aspect | Stress | Strain |
---|---|---|
Definition | Internal force per unit area within a material | Deformation as a ratio of change in length (or other dimension) to original length |
Formula | σ = F / A | ε = ΔL / L0 |
Unit | Pascal (Pa) or N/m² | Dimensionless (no units) |
Physical Meaning | Intensity of external/internal force | Measure of deformation |
Cause/Effect | Cause | Effect |
Measurement | Via force and area | Via change in dimensions |
Relationship: Stress-Strain and Hooke’s Law
Stress and strain are directly related within the elastic region of a material. According to Hooke’s Law, when a material is deformed within its elastic limit, the stress is proportional to the strain:
E here is the elastic modulus (often called Young’s modulus for tensile/compressive cases), which indicates the stiffness of the material. This law holds only until the material reaches its elastic limit. Beyond this, materials may deform permanently (plastic deformation), and the linear relationship no longer applies.
Understanding the Stress-Strain Curve
The stress-strain curve visually summarizes how a material responds to increasing loading. The initial part (elastic region) shows a straight-line relationship, starting from zero. The slope of this linear region is Young's modulus. When the material is loaded beyond the elastic region, it enters the plastic region, where deformation becomes permanent.
Materials like metals, polymers, or ceramics each have distinct stress-strain curves. Toughness, yield point, and ductility can all be analyzed using these curves.
Practical Example
A metal wire of original length 1 meter experiences a change in length of 2 millimeters when a force is applied. If the cross-sectional area is 2 × 10-6 m² and the applied force is 400 N, calculate the stress and strain.
- Stress: σ = F / A = 400 N / 2 × 10-6 m2 = 2 × 108 N/m2
- Strain: ε = ΔL / L0 = 2 mm / 1000 mm = 0.002
Such calculations are essential for predicting the behavior and safety of materials in practical applications.
Key Types of Stress and Strain
Type | Description | Common Example |
---|---|---|
Tensile | Pulls and stretches a material | Metal wire under tension |
Compressive | Shortens or squeezes a material | Concrete pillar under load |
Shear | Forces layers to slide past each other | Cutting paper with scissors |
Volumetric | Changes in the overall volume | Gas compressed in a cylinder |
Thermal | Due to temperature changes | Metal rod expanding when heated |
Applications and Measuring Techniques
Measuring stress and strain helps in material selection and safety testing. Stress is typically calculated from known forces and cross-sectional area, while strain is measured by checking the change in length or shape. Common tools include strain gauges, extensometers, and digital sensors.
By studying the stress-strain behavior, engineers and scientists ensure structures like bridges, buildings, or machine parts perform reliably under different loads.
Explore More on Vedantu
To build mastery, practice solving numericals on the stress-strain relationship, interpret tabulated data, and review stress-strain curves for different materials. Understanding these concepts will provide a strong foundation for further studies in mechanics, materials engineering, and structural analysis.
FAQs on Stress and Strain in Physics: Concepts, Types, and Formulas
1. What is the difference between stress and strain?
Stress is the force applied per unit area on a material, measured in N/m2 (Pa). Strain is the ratio of change in dimension (such as length) to the original dimension and is dimensionless. In summary:
- Stress = Force / Area (N/m2)
- Strain = Change in length / Original length (unitless)
2. What is the relation between stress and strain?
Stress and strain are related by Hooke’s Law within the elastic limit of a material:
- Stress = Young’s Modulus × Strain
- Formula: σ = E × ε, where σ = stress, E = Young’s Modulus, ε = strain.
3. What are the different types of stress and strain?
Stress Types:
- Tensile Stress: Pulls material apart
- Compressive Stress: Squeezes material
- Shear Stress: Parallel sliding forces
- Volumetric Stress: Acts in all directions
- Tensile Strain: Elongation
- Compressive Strain: Shortening
- Shear Strain: Angular deformation
- Volumetric Strain: Change in volume
4. What is Young's Modulus? How can it be calculated?
Young's Modulus (E) is a measure of the stiffness of a material; it relates stress and strain during elastic deformation.
- Formula: E = Stress / Strain
- Unit: N/m2 (Pascal)
- Used to calculate material rigidity and compare stiffness.
5. What is the stress-strain curve and what does it indicate?
The stress-strain curve graphically shows how a material deforms under increasing stress.
- Elastic region: Material returns to original shape
- Proportional limit: Follows Hooke’s Law (linear)
- Yield point: Permanent deformation begins
- Ultimate strength: Maximum stress endured
- Fracture point: Material breaks
6. What is Hooke’s Law and its limitations?
Hooke’s Law states that within the elastic limit, stress is directly proportional to strain.
- Expression: Stress = E × Strain
- Valid only in the elastic region (material returns to original state after stress)
- Not valid beyond the elastic limit—plastic deformation occurs
7. How do you calculate stress and strain numerically?
To calculate stress:
- Stress = Force / Area (N/m2)
- Strain = Change in length / Original length (dimensionless)
8. What is meant by elastic limit and plastic deformation?
Elastic limit is the maximum stress a material can withstand and still return to its original shape once the force is removed. Plastic deformation occurs when stress exceeds the elastic limit, causing permanent shape change even after removal of the force.
9. What are common units and dimensions used for stress and strain?
Stress: Unit is N/m2 (Pascal, Pa); Dimension is ML-1T-2.
Strain: It is dimensionless and has no unit since it is a ratio of lengths.
10. Give a real-life example where stress and strain concepts are applied.
Stress and strain are essential in engineering and construction.
- Example: Designing a bridge—engineers calculate the maximum stress the bridge material can handle and ensure the strain does not exceed the safe limit to prevent structural failure.
11. How is shear strain different from tensile and compressive strain?
Shear strain measures angular deformation due to forces acting parallel to a surface, whereas tensile strain is caused by stretching and compressive strain results from compression. Shear affects shape without much change in length, while tensile and compressive strains affect length.
12. What are the formulas for bulk modulus and shear modulus in relation to stress and strain?
Bulk modulus (K) measures a material’s resistance to uniform compression:
- K = -ΔP / (ΔV/V) (ΔP = change in pressure, ΔV = change in volume)
- G = Shear Stress / Shear Strain
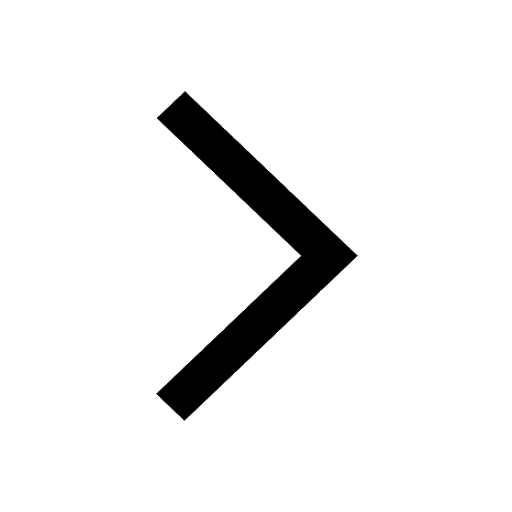
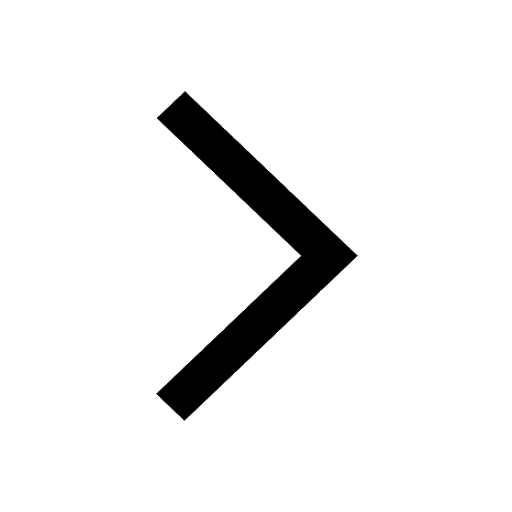
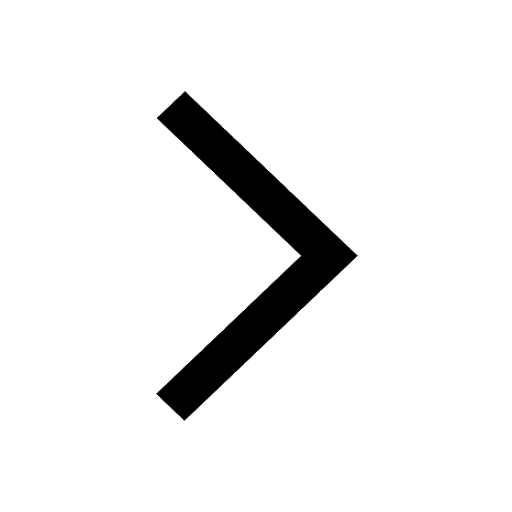
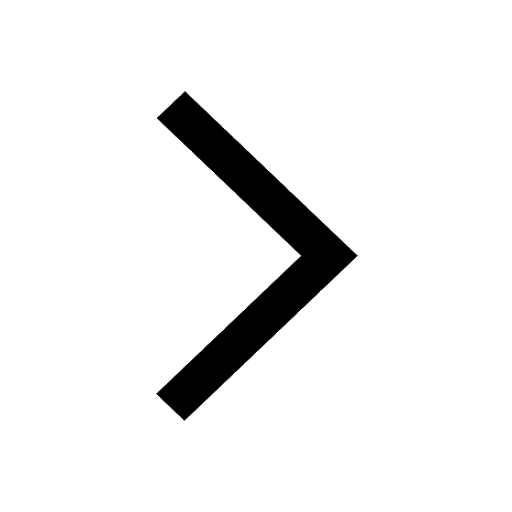
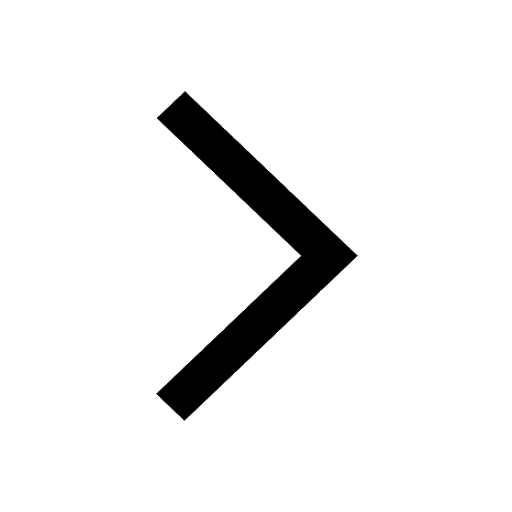
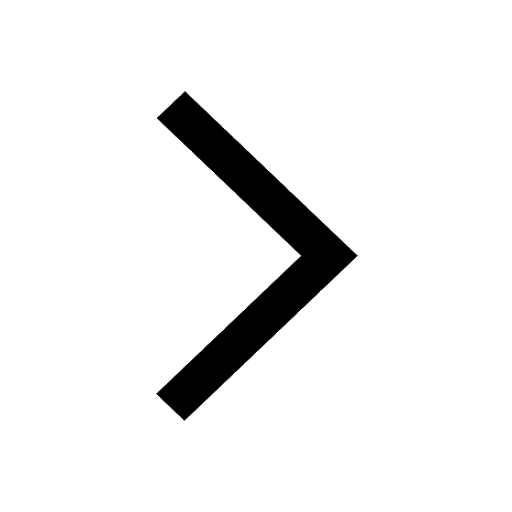
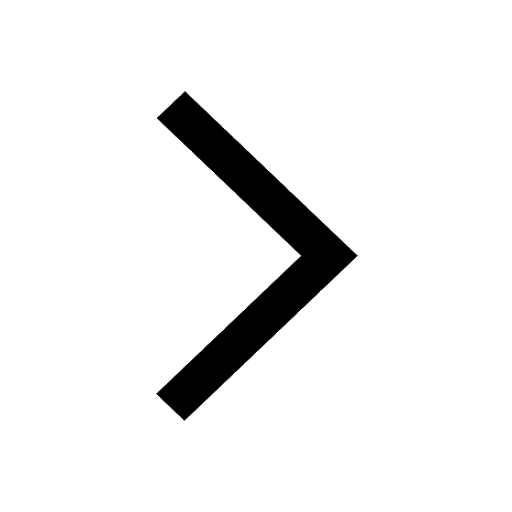
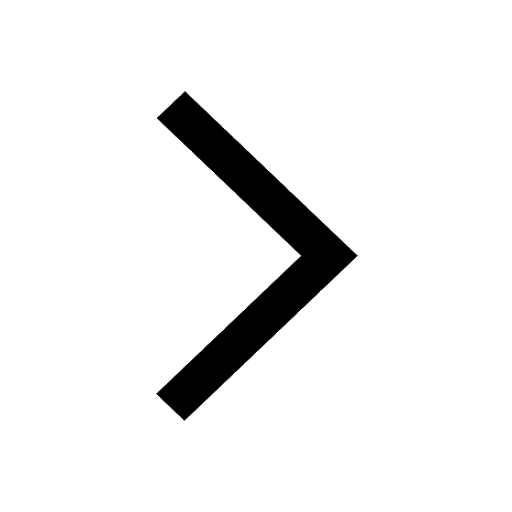
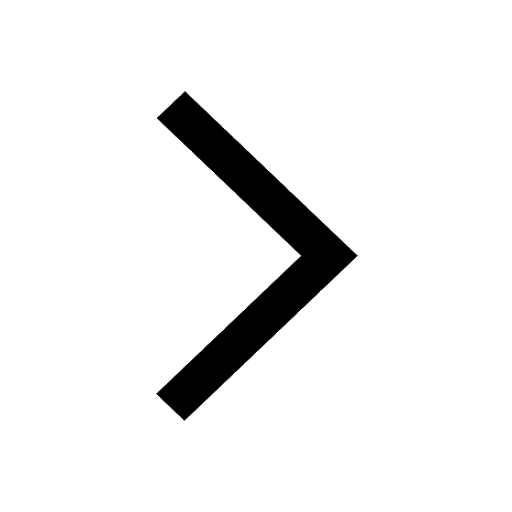
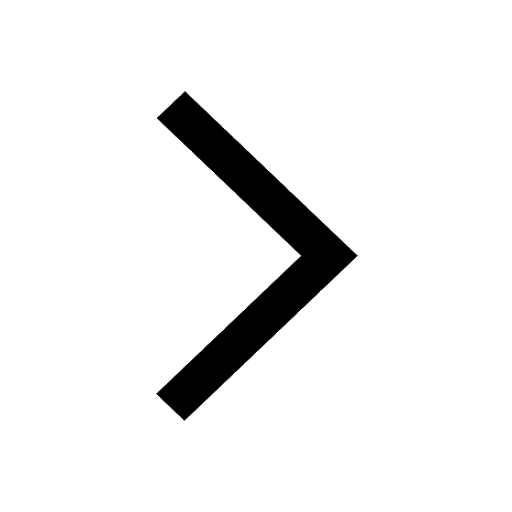
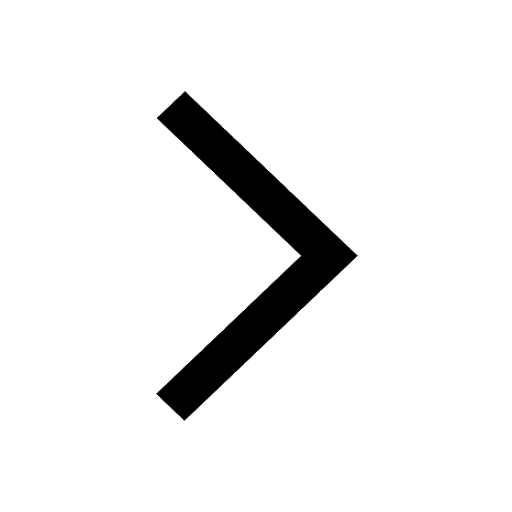
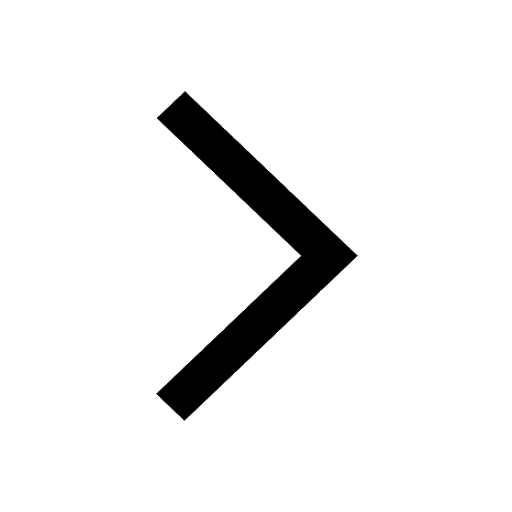
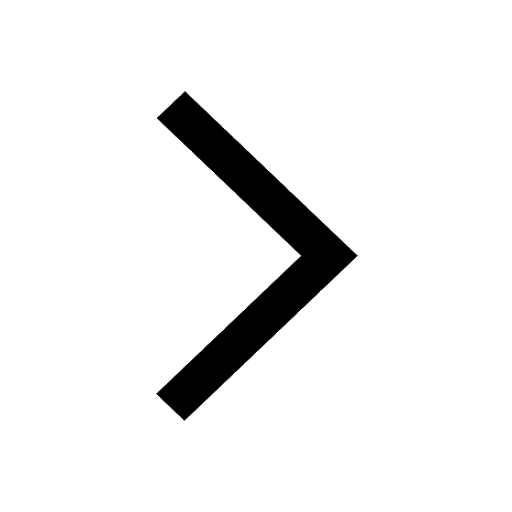
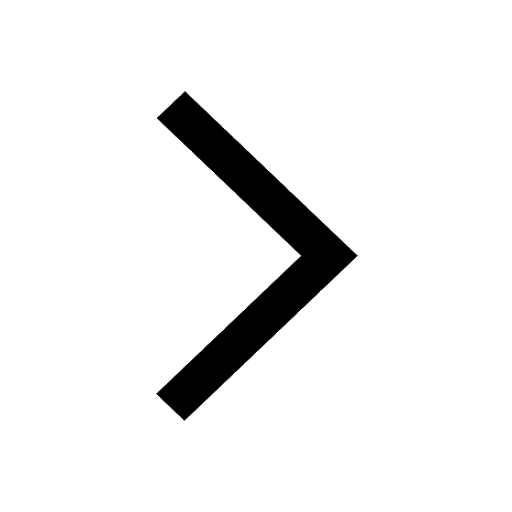
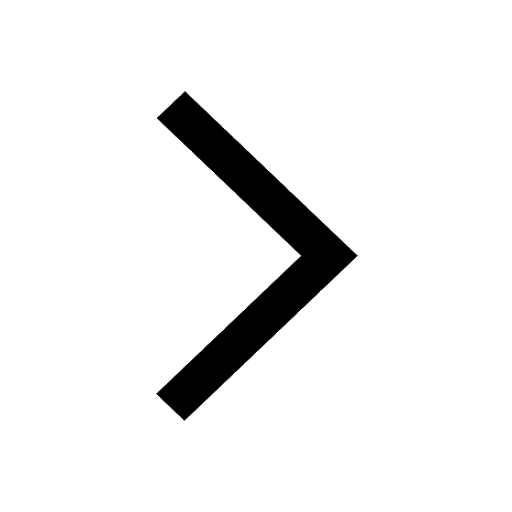
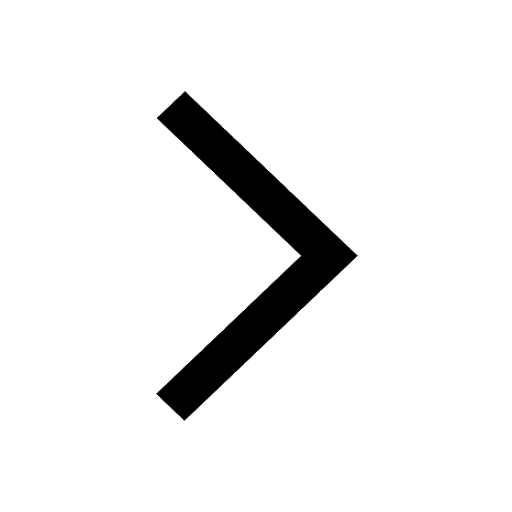
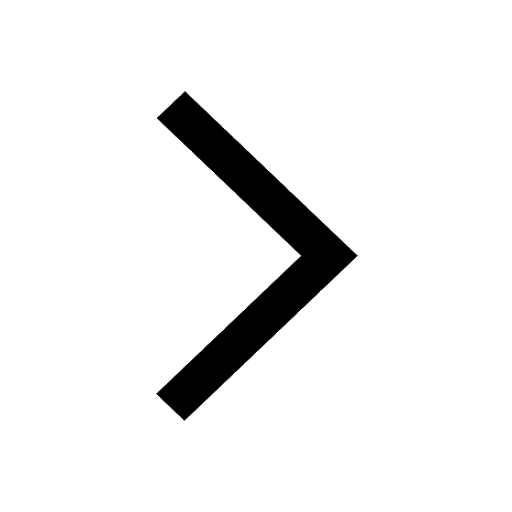
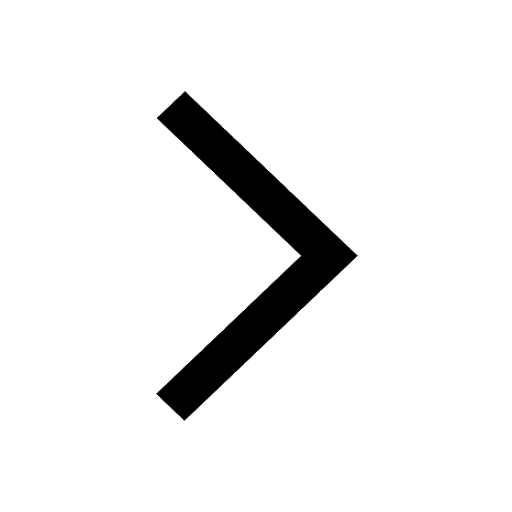