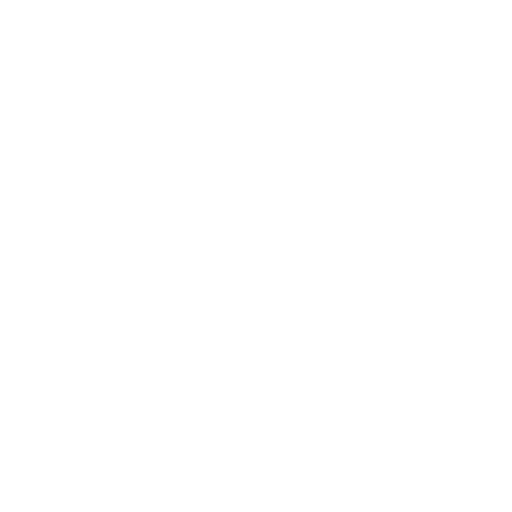

How Does an Electric Motor Work? Principle, Uses and Diagram
An electric motor is a device that transforms electrical energy into mechanical energy, mainly by making use of electromagnetic phenomena. Most electric motors operate by utilizing the interaction between an electric current and a magnetic field. The outcome is the development of a torque that turns the motor's rotor, enabling the conversion of energy to useful mechanical work.
The most common form of modern electric motor is the induction motor. This type uses straightforward construction and reliable principles, which are often seen in industrial and household applications. Understanding the operation and design of induction motors helps to grasp the broader principles behind all electric motors.
Principle of Operation of the Induction Motor
The core concept of the induction motor is based on electromagnetic induction. When a set of three-phase alternating currents flows through the stator windings, it produces a rotating magnetic field across the air gap of the machine. This rotating field is key to the motor's operation and is central to its ability to produce continuous torque and motion.
The stator windings can be arranged in a wye or delta configuration, adapting the machine for different requirements without changing the fundamental principle. As the magnetic field rotates, it interacts with the rotor inside the stator.
Working of the Induction Motor
When the stator windings are energized with three-phase AC supply, sinusoidal currents create a changing magnetic field. This field rotates through one complete revolution for each cycle of the supply frequency. For example, with a 60-hertz supply, the field rotates at 3,600 revolutions per minute (rpm).
The rotor, typically comprising a cylindrical iron core with conductors along its surface, is not directly connected to any power source. Instead, as the rotating magnetic field passes relative to the rotor conductors, it induces voltages in them. These induced voltages cause currents to flow, especially since the conductors are short-circuited at both ends.
The resulting rotor currents interact with the stator's magnetic field, generating a torque in the rotor. This torque causes the rotor to turn in the same direction as the rotating magnetic field. As the rotor accelerates, its speed approaches the field’s speed but remains slightly less—a phenomenon known as slip.
Important Terms and Concepts
Term | Description |
---|---|
Stator | The stationary outer part with windings through which AC flows. |
Rotor | The rotating part, consisting of iron core and conductors. |
Rotating Magnetic Field | A magnetic field that moves in a circular path, produced by stator windings. |
Slip | The small difference between the speed of the rotating field and the rotor’s speed. |
Step-by-Step: How an Induction Motor Produces Motion
- Three-phase AC current is supplied to the stator windings.
- This creates sinusoidally varying currents and a rotating magnetic field in the air gap.
- The moving field induces voltages in the rotor's conductors.
- Induced currents flow in the short-circuited rotor windings.
- Interaction between rotor currents and magnetic field generates a torque.
- The torque accelerates the rotor in the same direction as the magnetic field’s rotation.
- As the rotor speeds up, slip decreases until rotor torque equals load torque, reaching steady operation.
Key Formulas in Induction Motor Physics
Formula | Explanation |
---|---|
Synchronous Speed (Ns) = 120f/p | f = supply frequency (Hz); p = number of poles |
Slip (s) = (Ns - N) / Ns |
N = actual rotor speed; slip is a measure of speed difference |
Torque ∝ (Rotor Current) × (Strength of Magnetic Field) |
Torque is produced by interaction between induced current and the rotating magnetic field |
Applications and Usage
Three-phase induction motors are widely used due to their robustness and minimal maintenance. Typical voltage supply ranges from 230 volts (for 0.5 to 50 kW motors) up to 15 kilovolts (for much larger systems). These motors are popular in both household devices and industrial machinery.
The speed of the rotating field and thus the output speed of the motor can be selected by choosing the number of poles in the design. For instance, with a 60 Hz supply, a two-pole motor has a synchronous speed of 3,600 rpm, while motors with more pairs of poles run at lower synchronous speeds.
Sample Problem Approach
Step | What to do | Example |
---|---|---|
1 | Write supply frequency and number of poles | f = 50 Hz, p = 4 |
2 | Compute synchronous speed (Ns) | Ns = 120 × 50 / 4 = 1,500 rpm |
3 | Given actual rotor speed, calculate slip | If N = 1,440 rpm, s = (1,500 - 1,440) / 1,500 = 0.04 or 4% |
Types of Induction Motor Connections
Type | Configuration | Features |
---|---|---|
Wye (Star) | Neutral not externally connected | Common for balanced loads |
Delta | Triangle connection | Allows higher starting current |
Summary and Next Steps
Induction motors are crucial in transforming electrical power into mechanical movement by using rotating magnetic fields and induced currents. The small slip between field and rotor speeds enables efficient, reliable torque for many applications.
To deepen your understanding, explore related topics like Types of Motors, Differences between AC and DC Motors, and Magnetic Effects of Electric Current. For more on fundamental concepts and practice, visit these:
Practice applying slip, synchronous speed, and torque calculations, and consider building problem-solving skills by working through stepwise numerical examples.
FAQs on Electric Motor – Working Principle, Types, Diagram & Applications
1. How does an electric motor work?
An electric motor works by converting electrical energy into mechanical energy using electromagnetic principles. When a current-carrying conductor is placed inside a magnetic field, it experiences a force (as per Fleming’s Left Hand Rule), causing the motor’s coil to rotate and produce mechanical motion.
2. What are the main types of electric motors?
The main types of electric motors are:
- DC motors (run on Direct Current)
- AC motors (run on Alternating Current)
- Universal motors (work on both AC and DC)
- Stepper motors (precise motion in steps)
3. What is the working principle of an electric motor?
The working principle of an electric motor is based on the fact that a current-carrying conductor in a magnetic field experiences a force, causing rotation. This principle is implemented in motors to convert electrical energy into useful mechanical energy for various devices.
4. Can you explain Fleming's Left Hand Rule in the context of motors?
Fleming’s Left Hand Rule helps determine the direction of force on a conductor in an electric motor. Hold your left hand with thumb, forefinger, and middle finger at right angles:
- Forefinger points in the direction of the magnetic field
- Middle finger points in the direction of current
- Thumb points in the direction of force (motion)
5. What are the main parts of an electric motor?
The main parts of a simple electric motor are:
- Armature (rotor)
- Commutator
- Brushes
- Magnetic field (permanent magnets or electromagnets)
- Power supply
6. What are the uses of electric motors in daily life?
Electric motors are widely used in daily life, including:
- Household appliances (fans, mixers, washing machines)
- Vehicles (electric cars, motorbikes, trains)
- Industrial machines and conveyor systems
- Pumps and compressors
- Robotics and medical devices
7. What is the difference between an electric motor and an electric generator?
An electric motor converts electrical energy into mechanical energy (motion), while an electric generator converts mechanical energy into electrical energy. Motors use the motor effect (Lorentz force), whereas generators use electromagnetic induction.
8. What is the difference between AC motors and DC motors?
AC motors operate on alternating current, are common in household and industrial applications, and are known for stable operation. DC motors run on direct current, are often used in low-voltage devices, and provide easy speed control. The choice depends on the power source and operational requirements.
9. How is horsepower (HP) related to watts in electric motors?
Horsepower (HP) and watts (W) are both units of power. The relation is:
1 HP = 746 W. To convert from watts to horsepower, divide the power in watts by 746.
10. Which formula is used to calculate the force experienced by a conductor in a motor?
The force on a current-carrying conductor in a magnetic field is given by:
F = B I l
Where:
- F = Force (in Newtons)
- B = Magnetic field strength (in Tesla)
- I = Current (in Amperes)
- l = Length of conductor in the field (in meters)
11. What is the role of efficiency in an electric motor?
Efficiency in an electric motor measures how much input electrical energy is converted into useful mechanical energy. It is calculated as:
Efficiency (%) = (Mechanical Power Output / Electrical Power Input) × 100
Higher efficiency means less energy is lost as heat, improving motor performance.
12. What are common reasons an electric motor might fail or stop working?
Common reasons for electric motor failure include:
- Overheating due to prolonged use or overload
- Worn-out brushes or commutators
- Electrical short circuits or insulation breakdown
- Faulty bearings or mechanical jams
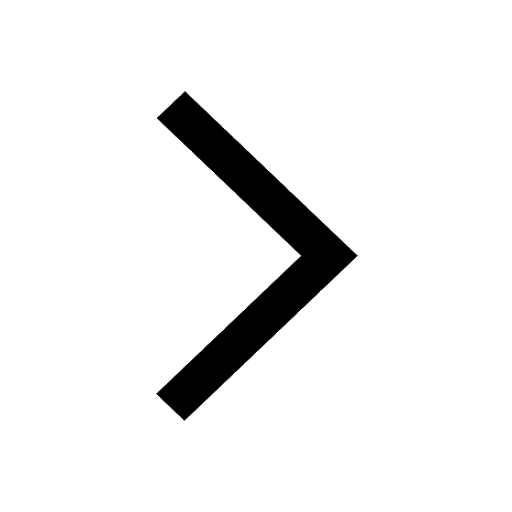
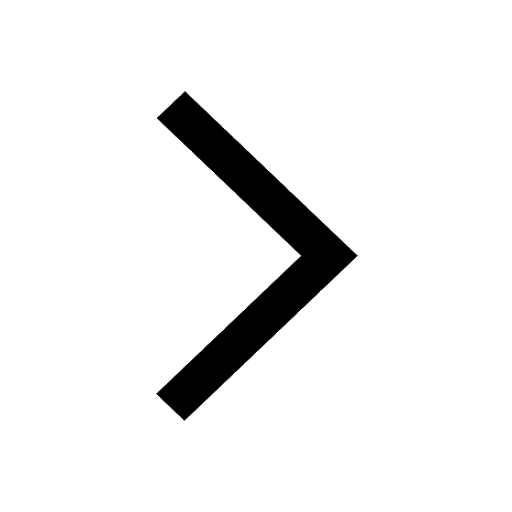
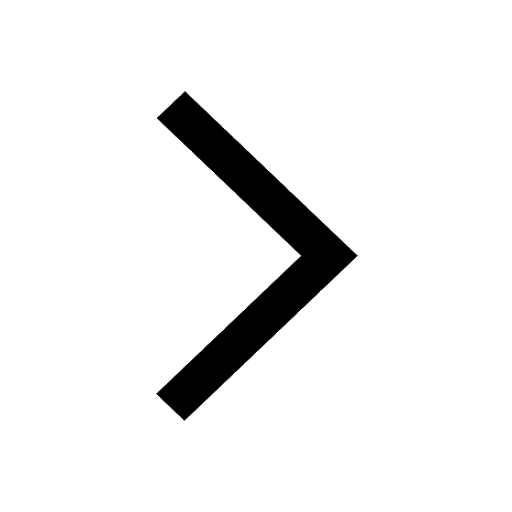
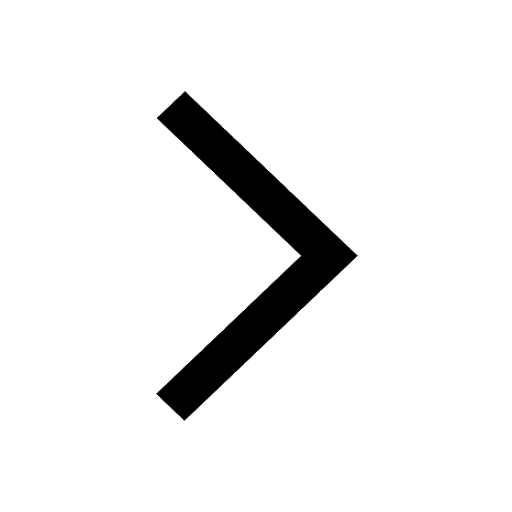
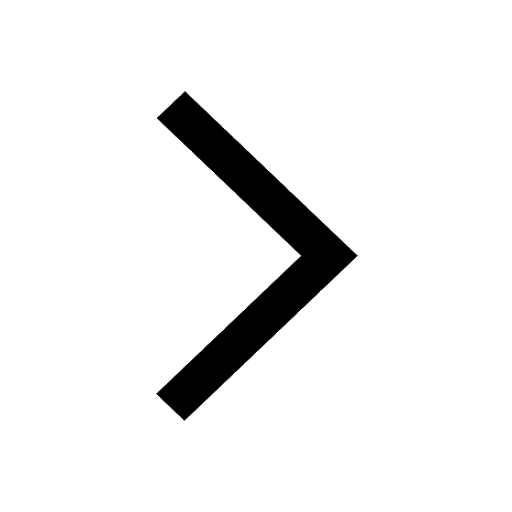
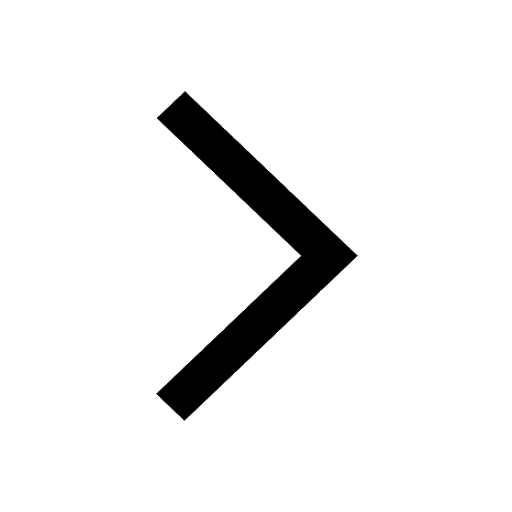
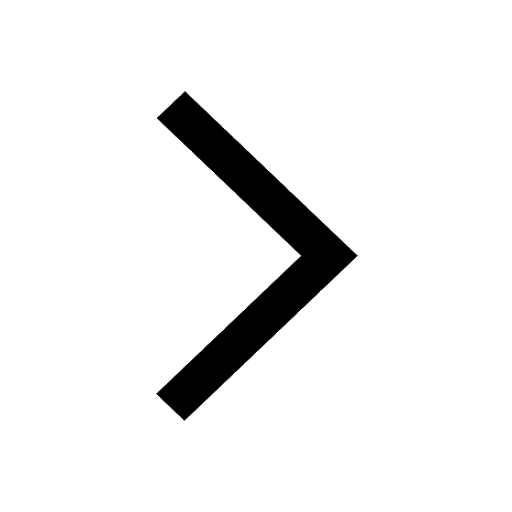
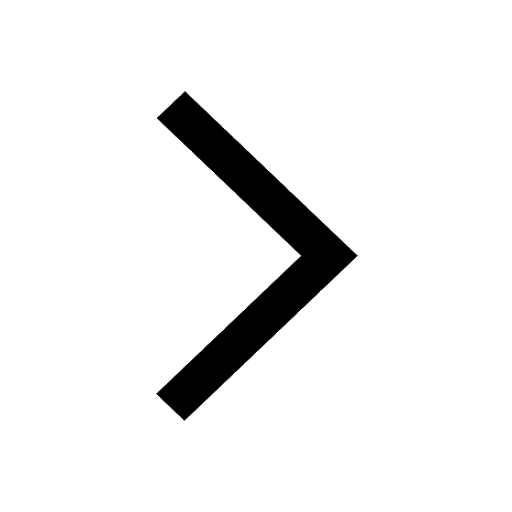
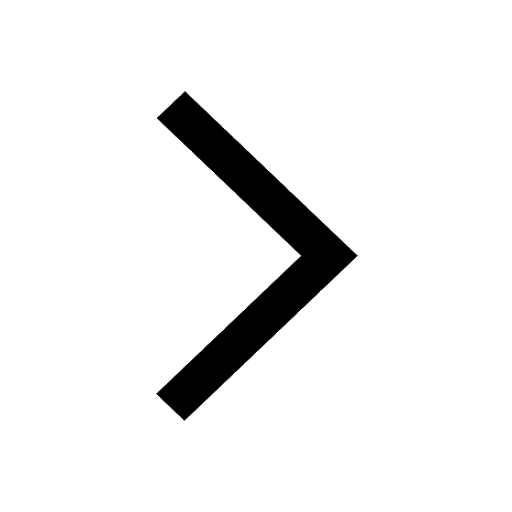
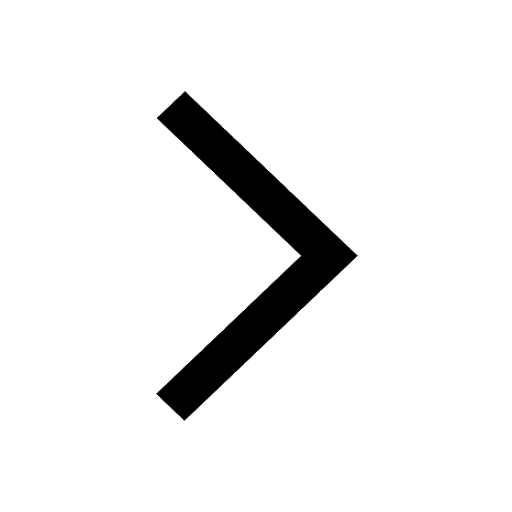
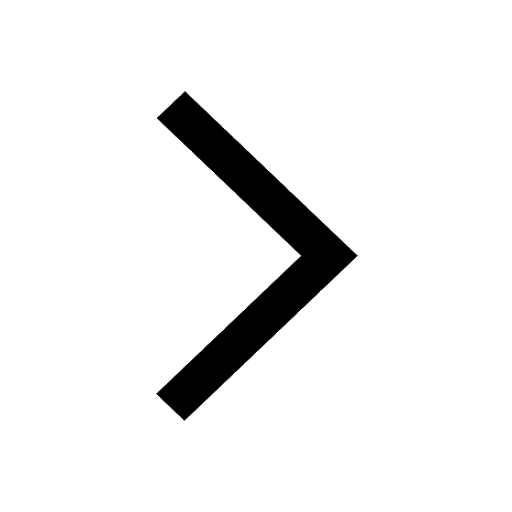
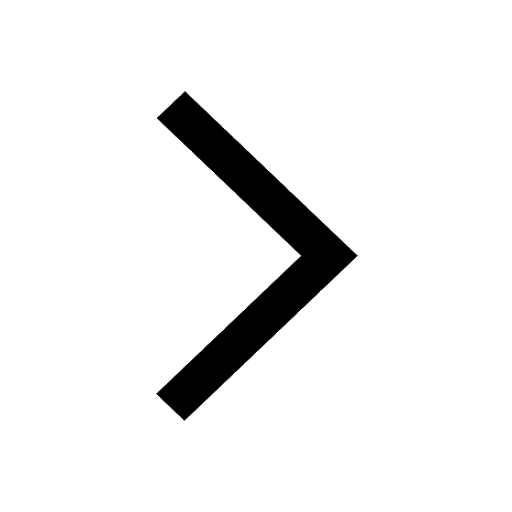
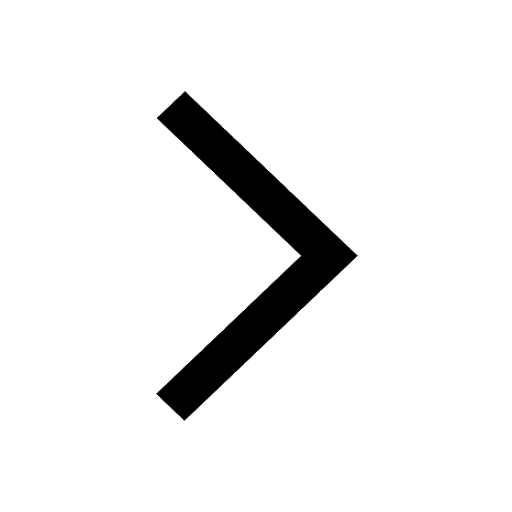
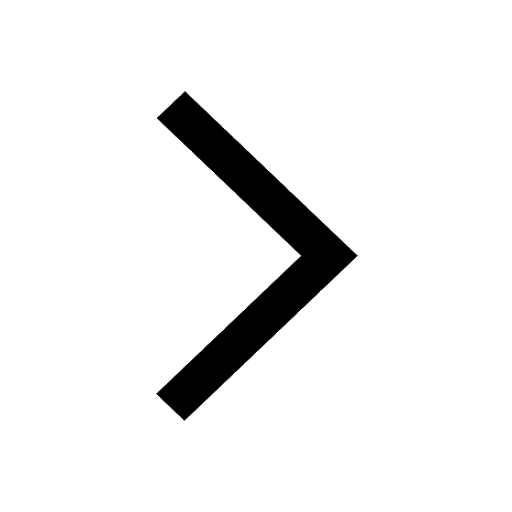
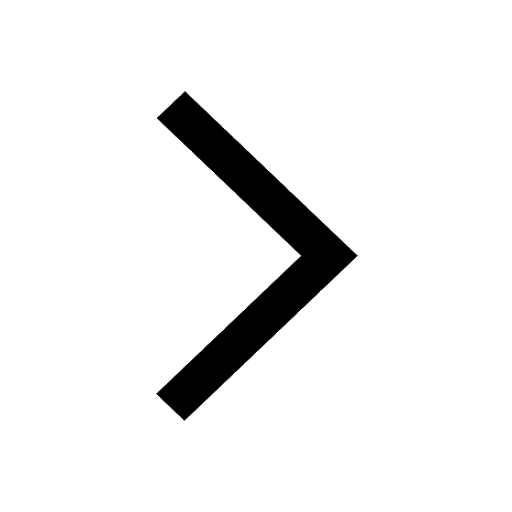
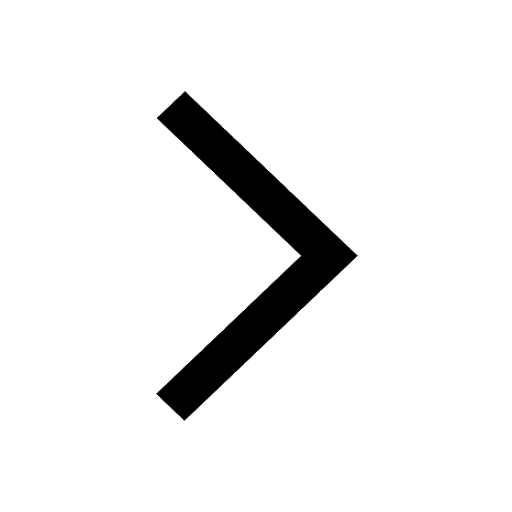
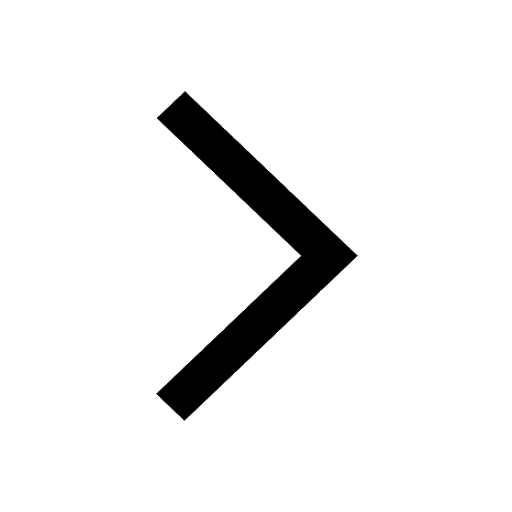
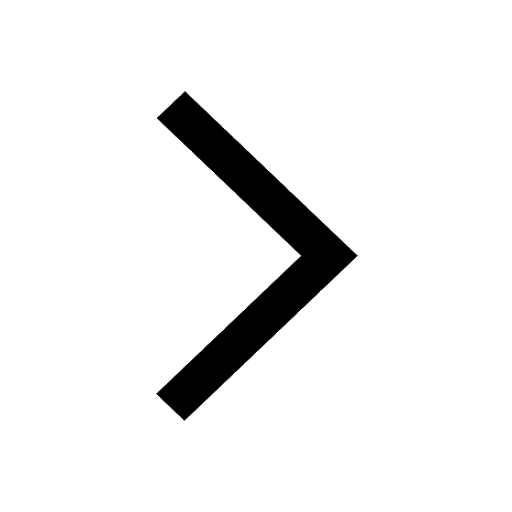