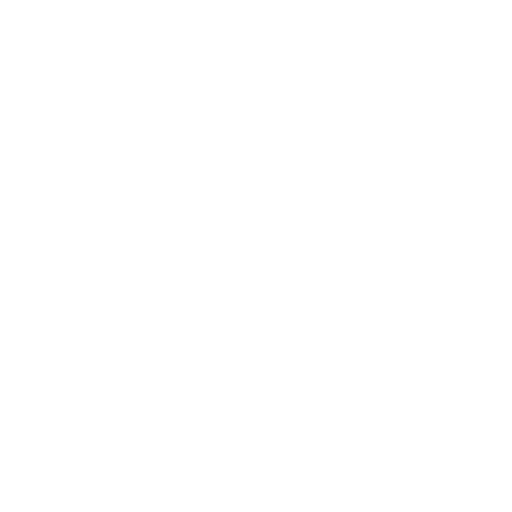

How Does Compressive Stress Affect Materials in Physics?
When force is applied to an elastic band it stretches and when it does stretch it tends to undergo stress during the stretching. When the stress on the elastic band has reached its limit it tends to break and hence releasing the stress that was held by the elastic band. This stress is one of the factors that give it a shape. However, not every object is elastic in nature. Some are rigid and hence cannot be easily malleated even after providing an ample amount of stress to the material. One of the typical examples is a ping-pong ball which is quite brittle as it is made of plastic. Under stress, it tends to break and now holds a shape.
(Image will be uploaded soon)
Compressive stress is the restoring strain developed because of pressure or force applied on a material to deform it, thereby causing a reduction of its volume. This capability of materials to withstand such compression is known as compressive strength. Here, we will discuss these two essential terminologies in detail.
What Is Compressive Stress?
It is the measure of restoring stress developed in a body as a result of force applied on a material for the intention of deforming it. The maximum force at which materials deform and their volume is reduced, is known as compressive stress. The value of stress may differ from one element to another. Let us understand this by taking two scenarios –
In case this force is applied to brittle materials, the material breakdowns into smaller particles because of the sudden release of energy.
In case the material is ductile, it can be compressed easily.
What is Compressive Strength?
It is the measure of the capacity of a material to withstand the external force applied to it with an intention to deform it. Once the compressive strength limit of a substance is attained, it may fracture or deform.
Therefore, as per compressive strength meaning, brittle materials are more likely to have higher compressive strength than ductile ones.
Kinds of Stress
One can deform a solid by applying external force. However, it is possible by only three ways as mentioned below.
Tensile Stress – It is the equal force applied on a body perpendicular to its cross-sectional area to deform it.
Compressive Stress Definition – The solid is compressed by applying an external force. In response, the restoring force is produced in the body, which is known for compressive stress.
Shearing Stress – A tangential force developed in the solid body because of the application of two equal & opposite external forces parallel to its cross-sectional area is known as the shearing stress.
Formula
The compressive stress formula can be written as
σ = F/A
Where,
σ is compressive stress.
A is the unit area of a solid body.
F is a compressive force.
This can also be used as the compressive strength formula as it is the limit at which the solid material deforms.
Units and Dimensions
SI units for compressive stress or compressive strength units can be expressed as Nm-2 or Pascal (Pa).
The dimensional formula for the same will be [M L-1 T-2].
Tensile Stress vs Compressive Stress
Questions to Answer
1.A material pulled with tension force experiences a reduction in the compressive strength.
True
False
Ans: a
2.Choose the material which has higher compressive strength than tensile strength.
Fibreglass
Silica
Cast iron
Alumina
Ans: a
3.Calculate compressive of a cylindrical body with a 2cm diameter and applied force of 10 N.
450 kN/m2
678kN/m2
875 kN/m2
796 kN/m2
Ans: d
While these concepts help you score high grades in academics, these can also have practical applications. Therefore, strengthen your knowledge of the basic concepts of Physics and ensure fulfilling your academic pursuits.
Download the Vedantu app now and delve deep into the topic as you study our notes prepared by expert tutors. We ensure these are prepared lucidly so that you can grasp the topic quickly.
Types of Test that is Used to Test Compressive Stress
The compressive stress test will allow the determination of the behaviour of a material when it is exposed to a huge amount of compressive stress. The three types of tests can be provided as follows:
Flexure test
Crushing test
Spring test
Conclusion
Compressive strength can be calculated using the ratio of the maximum force applied on a solid body to its cross-sectional area. It is the maximum compressive stress experienced by a body before deformation. Compressive Stress is extremely critical in the domain of designing structures and provides the retaining strength or capability of materials like concrete, etc.
FAQs on Compressive Stress Explained: Definition, Formula & Applications
1. What is compressive stress as explained in Physics?
Compressive stress is the internal restoring force per unit of cross-sectional area that develops within a material when it is subjected to external forces that push on it, causing it to compress or shorten. It is a measure of how the material resists being squeezed. The material pushes back against the compression to maintain its original shape.
2. What is the formula to calculate compressive stress, and what are its SI unit and dimensional formula?
The formula for compressive stress (σ) is the ratio of the applied compressive force (F) to the cross-sectional area (A) over which the force is applied.
The formula is: σ = F / A
- The SI unit for compressive stress is Newtons per square metre (N/m²) or Pascals (Pa).
- The dimensional formula is [M L⁻¹ T⁻²].
3. How does compressive stress differ from tensile stress?
Compressive stress and tensile stress are opposite in nature. The key differences are:
- Nature of Force: Compressive stress is caused by a pushing force that squeezes an object, while tensile stress is caused by a pulling force that stretches it.
- Effect on Length: Compressive stress leads to a decrease in the object's length, whereas tensile stress leads to an increase in its length (elongation).
- Strain Convention: The strain associated with compressive stress is considered negative, indicating a reduction in dimension. The strain for tensile stress is positive.
4. What are some real-world examples of compressive stress?
Compressive stress is a fundamental concept in engineering and everyday life. Some common examples include:
- The pillars and columns of a building that support the weight of the structure above them.
- The legs of a chair experiencing a compressive force when a person sits on it.
- A car's shock absorbers, which compress to absorb the impact from bumps on the road.
- The force used to crush a soda can.
5. Why do brittle and ductile materials respond differently to compressive stress?
The different responses are due to their internal atomic structures. Ductile materials, like steel, can undergo significant plastic deformation before fracturing; under compression, they tend to bulge or barrel outwards. In contrast, brittle materials, like concrete or glass, have very little to no plastic deformation. When their compressive strength limit is reached, they fail suddenly by shattering or cracking.
6. How are compressive stress and compressive strain related to each other?
Compressive stress and compressive strain are directly related. Compressive stress is the internal force resisting compression, while compressive strain is the measure of the deformation itself (the ratio of the change in length to the original length). According to Hooke's Law, within the elastic limit of a material, compressive stress is directly proportional to compressive strain. This relationship is defined by the material's Young's Modulus.
7. What does the compressive stress-strain curve for a material reveal about its properties?
The compressive stress-strain curve is a graph that shows a material's behaviour under a compression test. It reveals several key properties:
- Elastic Limit: The point up to which the material will return to its original shape after the stress is removed.
- Young's Modulus: The slope of the initial, linear part of the curve, which indicates the material's stiffness.
- Yield Strength: The point where the material begins to deform plastically (permanently).
- Ultimate Compressive Strength: The maximum compressive stress the material can withstand before it begins to fracture or fail.
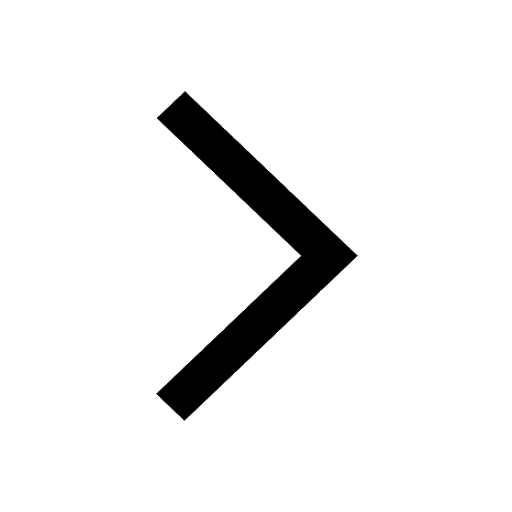
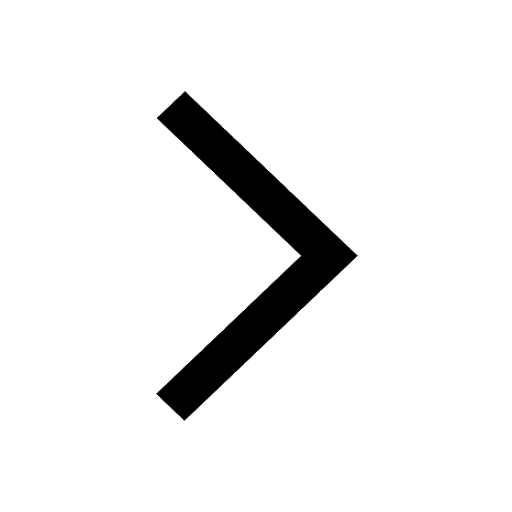
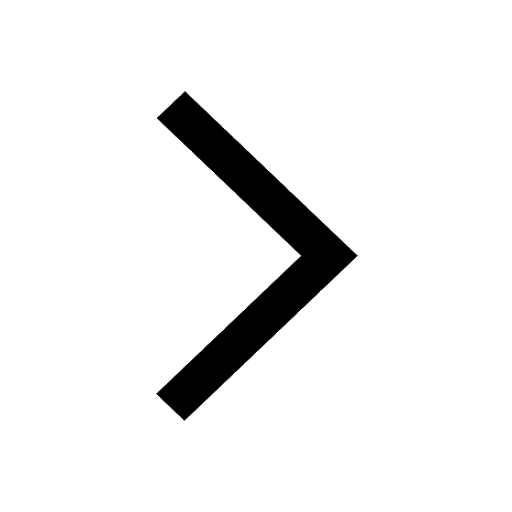
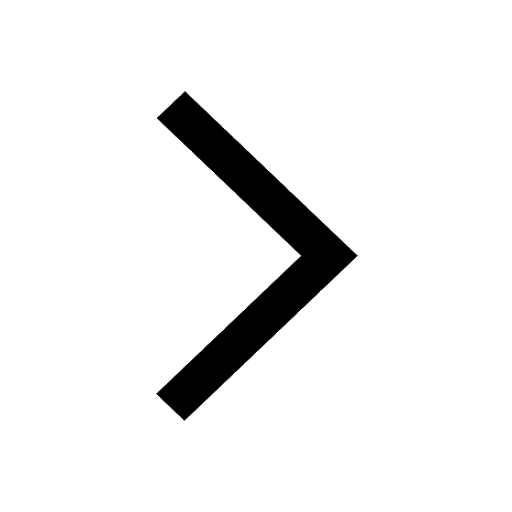
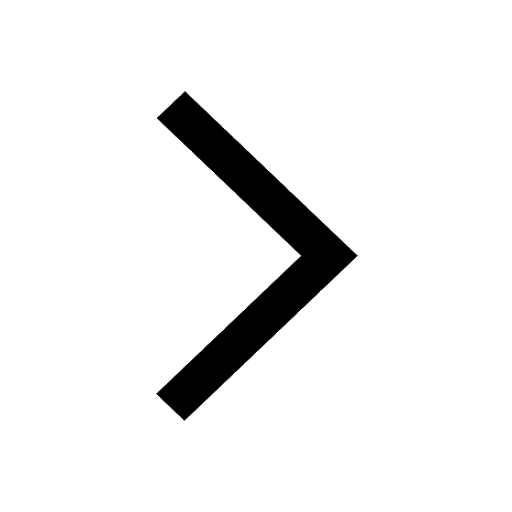
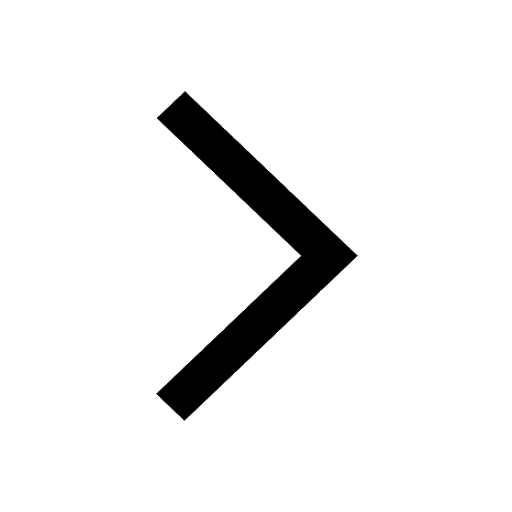
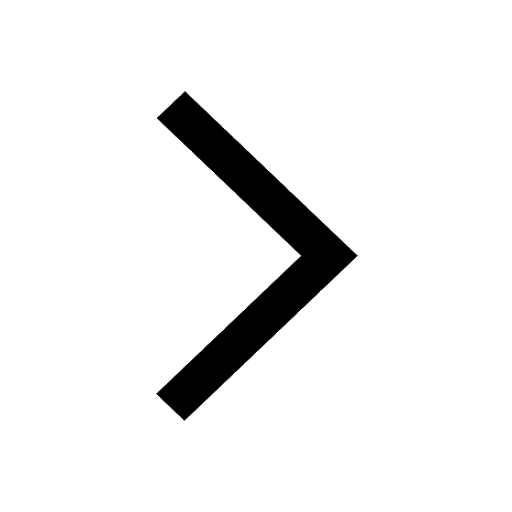
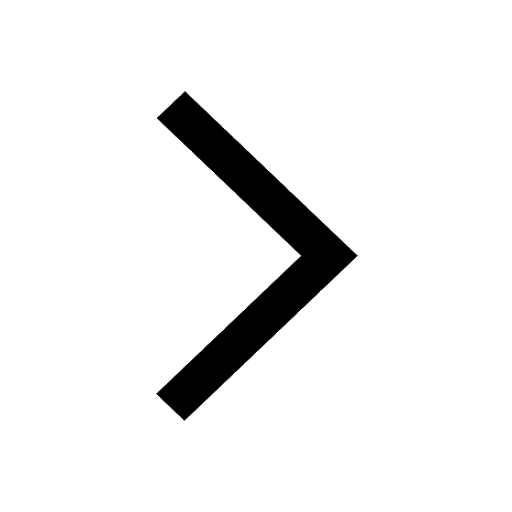
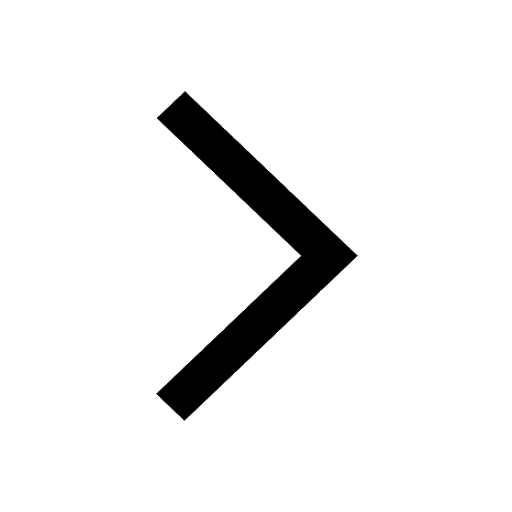
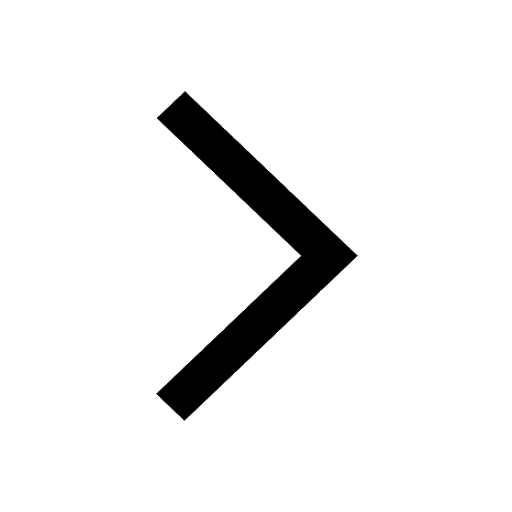
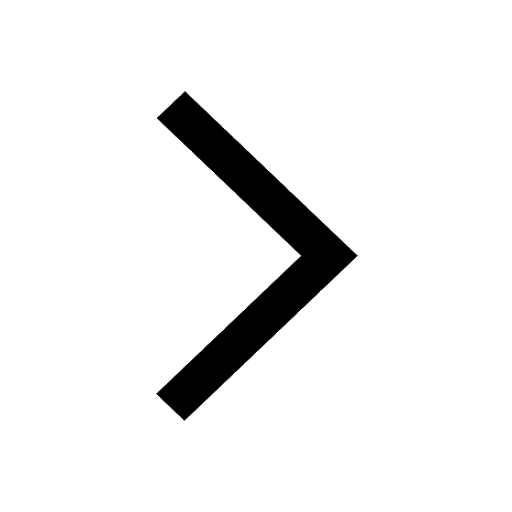
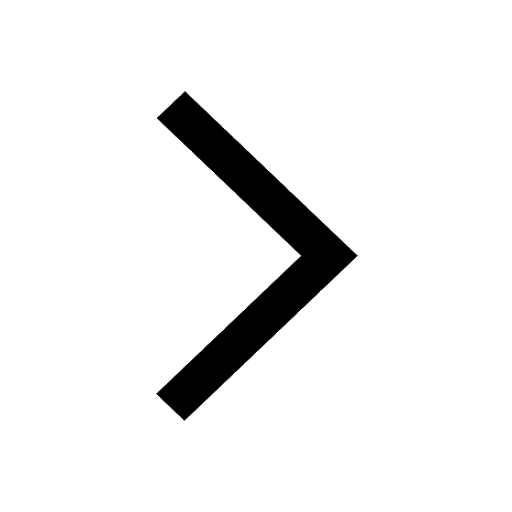
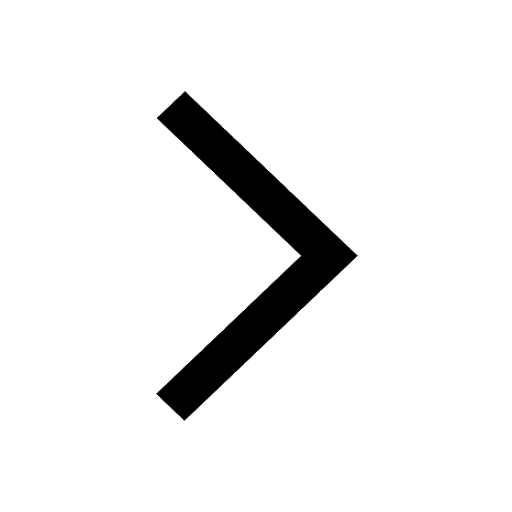
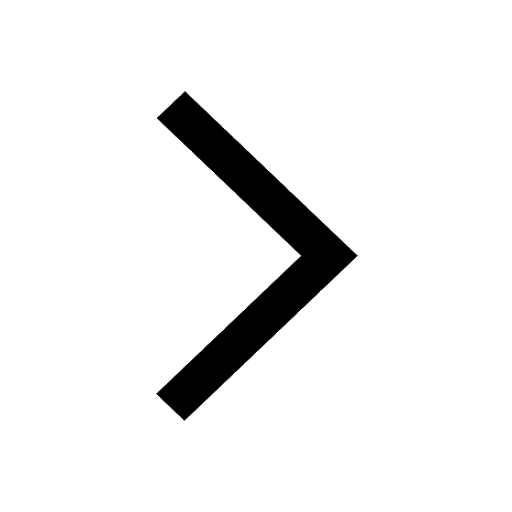
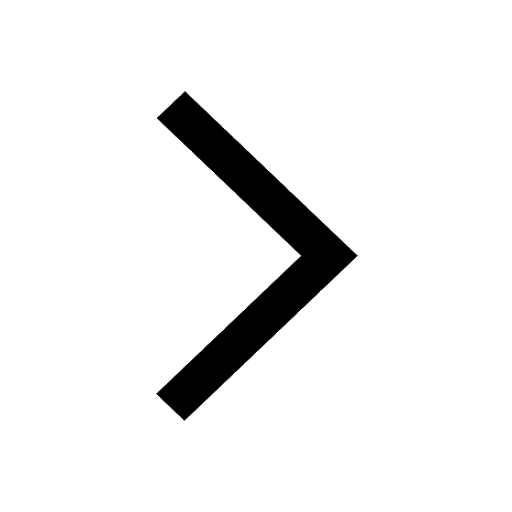
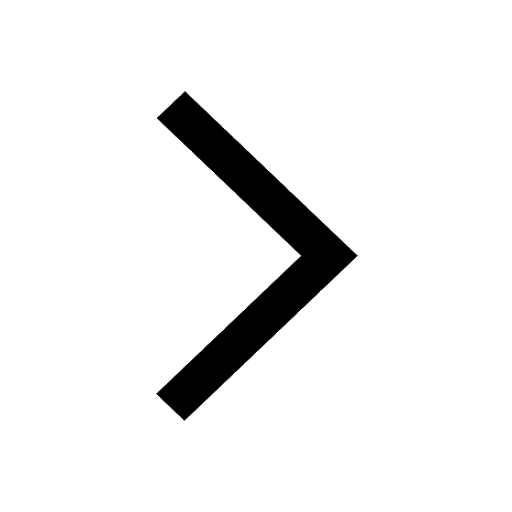
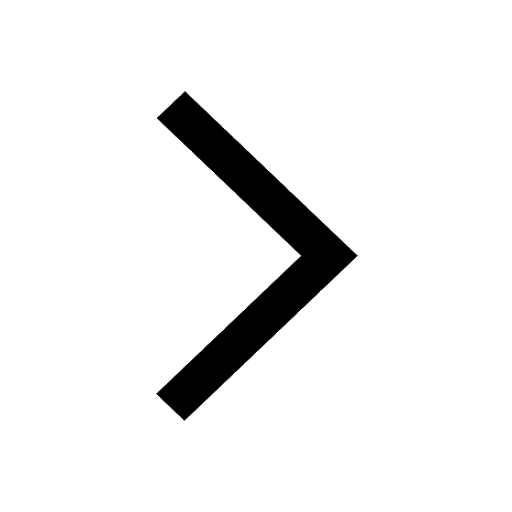
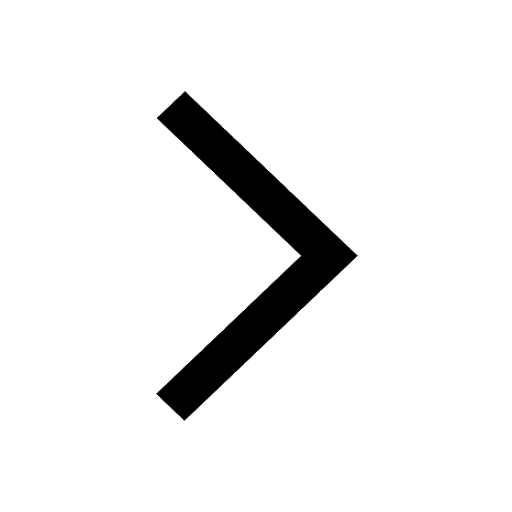