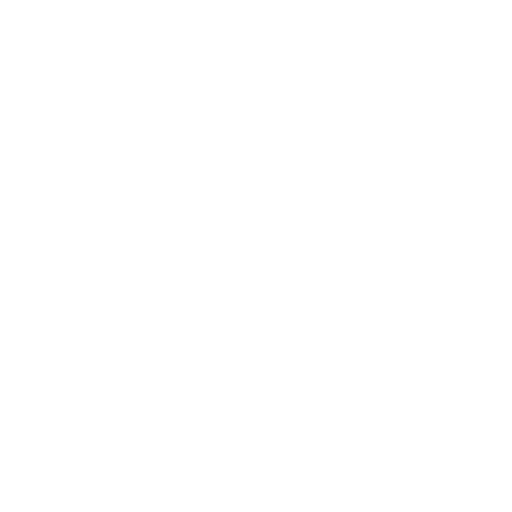

Rolling Friction vs Sliding and Static Friction: Key Differences and Applications
Rolling friction is a type of resistance force experienced when an object such as a ball, wheel, or cylinder rolls over a surface. Unlike sliding or static friction, rolling friction mainly arises from deformations in the surfaces in contact. When a wheel or ball rolls over another surface, both the object and the surface may deform slightly, and this energy loss due to the deformation is the main cause of rolling resistance.
Understanding Rolling Friction
Rolling friction, sometimes called rolling resistance, acts to oppose the motion of a rolling body. Its magnitude is usually much less than sliding friction for the same pair of materials. For example, a car tire rolling along a road encounters much less friction compared to dragging the same tire without rolling.
If both the rolling body and the surface are perfectly rigid (idealized scenario), there would be no rolling resistance. In real-life situations, energy losses occur mainly through elastic or inelastic deformation, roughness, and tiny slip regions in the contact area.
Empirical Laws and Behavior
Rolling friction follows certain empirical laws, similar to sliding friction. These include:
- The rolling friction force is directly proportional to the applied load.
- It varies inversely with the radius of curvature of the rolling object (smaller wheels have higher rolling resistance).
- Rolling friction is less on smoother surfaces than on rough ones.
- Static friction (preventing motion) is generally higher than kinetic (motion) friction, and rolling friction is usually the lowest of all three.
Formula for Rolling Friction
Rolling friction is most commonly calculated as:
where Fr is the rolling friction force, μr is the coefficient of rolling friction (a dimensionless constant dependent on materials and geometry), and N is the normal (perpendicular) load.
For cases involving significant surface deformation or different size wheels, modified versions of this formula include factors like wheel radius or sinkage depth.
Step-by-Step Problem Approach
To solve rolling friction problems, follow these steps:
- Identify the normal force (N), usually found by multiplying mass by gravitational acceleration if the object rests on a horizontal surface.
- Find the coefficient of rolling friction (μr). This value may be given in the problem or sourced from standard tables.
- Apply the formula: Fr = μr × N to calculate the resistive force.
- If required, plug this value into further equations to find acceleration, velocity, or work done against rolling friction.
Key Example
Suppose a solid steel ball with a mass of 3 kg is rolling on a hard surface. The normal force (N) equals its weight, or 3 × 9.8 = 29.4 N. If the coefficient of rolling friction (μr) is 0.001, the rolling friction force is Fr = 0.001 × 29.4 = 0.0294 N.
Type of Friction | How It Occurs | Typical Magnitude | Example |
---|---|---|---|
Static Friction | Prevents the start of motion between two surfaces at rest | Highest | Box not moving on floor |
Sliding (Kinetic) Friction | Objects moving across each other without rolling | Lower than static, higher than rolling | Book sliding on a table |
Rolling Friction | Object rolls over a surface (wheel, ball) | Lowest | Tire rolling on road |
Why Rolling Friction Is Usually Small
For practical applications, rolling friction is much smaller than sliding friction. This allows objects such as carts, cars, or suitcases with wheels to move more easily compared to dragging or sliding them. The main reason is that the area of contact under rolling is limited and less energy is dissipated in deformations.
However, the rolling resistance increases if either surface is soft, the wheel is small in diameter, or if the surface and wheel are rough or heavily loaded.
Physical Mechanism | Role in Rolling Friction |
---|---|
Elastic Deformation | Energy is lost when surfaces deform and recover; primary cause |
Plastic Deformation | Permanent surface grooves increase resistance |
Surface Roughness | Imperfections add micro-slips, increasing overall friction |
Common Examples of Rolling Friction
- Ball bearings in machines, allowing shafts to rotate smoothly
- Bicycles and cars moving on roads
- Train wheels on steel rails (with very low rolling resistance)
- A marble rolling on a flat surface
Key Formula | Description |
---|---|
Fr = μr × N | Rolling friction force for most practical situations |
μr = Fr / N | Finding the coefficient if measurements are known |
Preparation and Practice
To reinforce your understanding of rolling friction:
- Practice calculation-based questions using the formula Fr = μr × N.
- Compare rolling friction with sliding and static friction using typical examples from daily life.
- Explore how changes in surface properties, wheel size, or material type affect rolling resistance.
Further Learning and Resources
- Friction: Concepts and Types
- Frictional Force Explained
- Understanding Rolling Resistance
- Sliding Friction and Applications
- Friction in Automobiles
FAQs on Rolling Friction in Physics: Formula, Differences & Everyday Examples
1. What is rolling friction with example?
Rolling friction is the resistive force that opposes the motion when an object rolls over a surface. For example, when a ball or a tire moves across the ground, rolling friction acts at the point of contact to resist its motion.
2. How to calculate rolling friction?
The rolling friction force (Fr) can be calculated using the formula: Fr = μr × N, where μr is the coefficient of rolling friction, and N is the normal reaction force.
3. What is the coefficient of rolling friction?
The coefficient of rolling friction (μr) is a dimensionless constant that represents the degree of resistance to rolling motion between two surfaces. It is typically much smaller than the coefficients for static or sliding friction.
4. What are real-life applications of rolling friction?
Rolling friction is found in many daily applications, such as:
- Movement of car tires on roads
- Bicycle wheels rolling on pavements
- Trains running on steel tracks
- Ball bearings in machines
- Marbles rolling on floors
5. How does rolling friction differ from sliding friction?
Rolling friction occurs when an object rolls over a surface, while sliding friction happens when two surfaces slide against each other. Rolling friction is usually much smaller than sliding friction, which makes rolling objects easier to move than sliding ones.
6. What factors affect rolling friction?
Rolling friction is affected by several factors:
- Material and surface properties (hardness and smoothness)
- The radius of the rolling object
- Normal reaction force
- Deformation of the rolling object and surface
7. Why is rolling friction less than sliding friction?
Rolling friction is less than sliding friction because rolling contact involves less actual surface area in motion and less deformation, resulting in lower resistance compared to the continuous shearing involved in sliding.
8. What is the SI unit of rolling friction?
The SI unit of rolling friction force is the Newton (N). The coefficient of rolling friction, μr, is dimensionless (it has no unit).
9. Can rolling friction ever be greater than sliding friction?
In practical situations, rolling friction is almost always significantly less than sliding friction. However, in rare cases with extreme surface deformation or soft materials, rolling friction may approach sliding friction levels, but this is uncommon in standard scenarios.
10. State the formula for the coefficient of rolling friction.
The coefficient of rolling friction is given by: μr = Fr / N, where Fr is the rolling friction force and N is the normal reaction force.
11. Give two differences between static friction and rolling friction.
Difference 1: Static friction acts when an object is at rest, preventing motion; rolling friction acts when an object is rolling over a surface.
Difference 2: Static friction is usually much higher in magnitude than rolling friction, making it harder to initiate movement than to keep an object rolling.
12. List 3 ways to reduce rolling friction in machines.
Rolling friction can be reduced by:
- Using harder and smoother materials for rolling surfaces
- Lubricating contact surfaces to minimize deformation
- Increasing the diameter of wheels or rollers to decrease deformation at the contact point
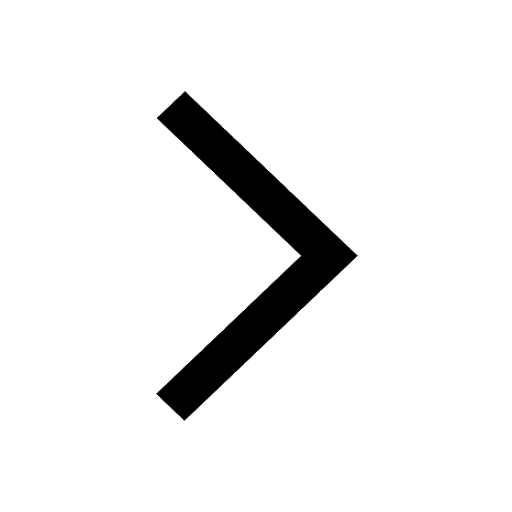
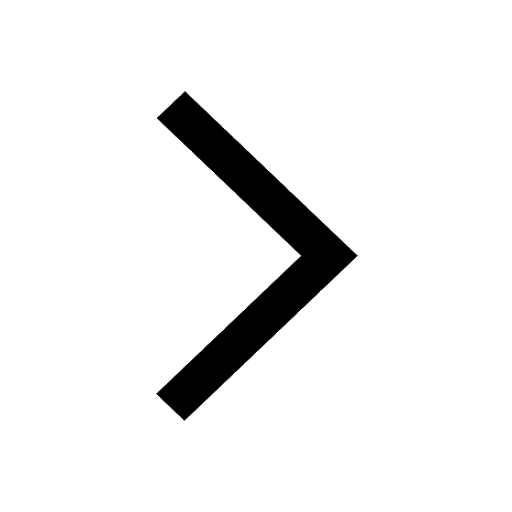
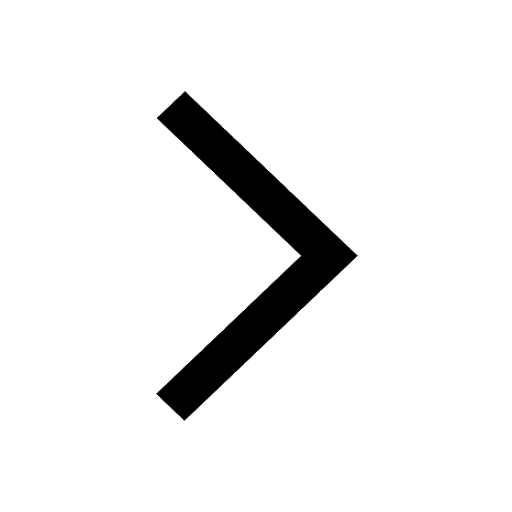
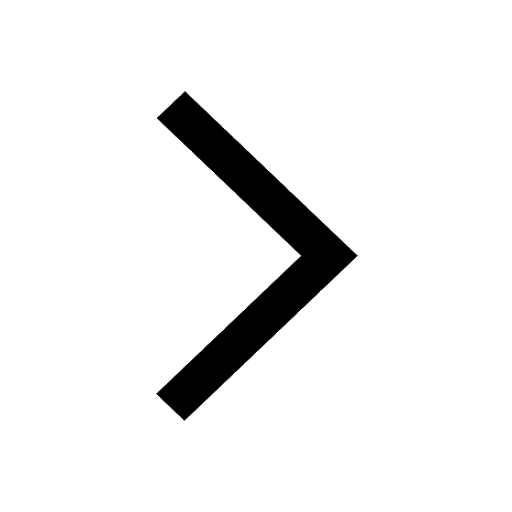
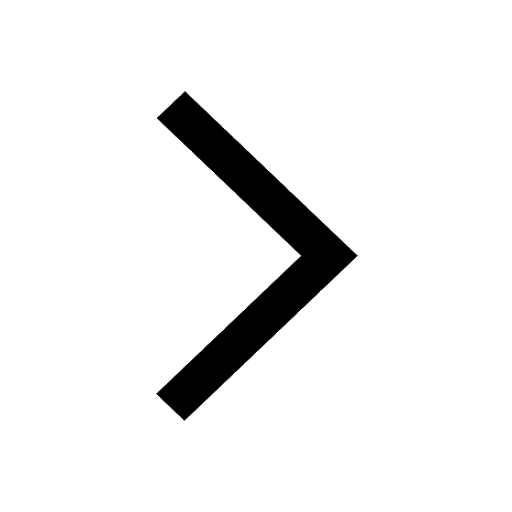
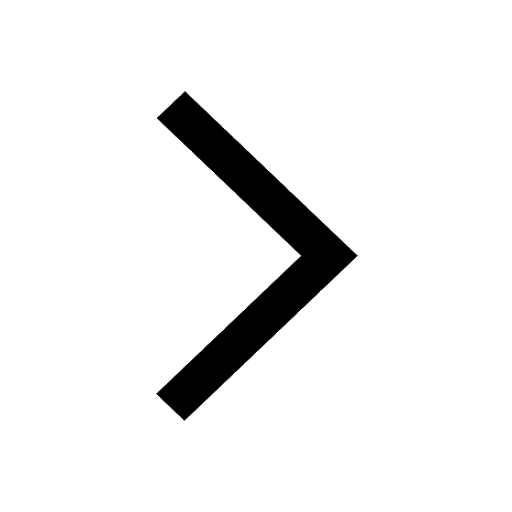
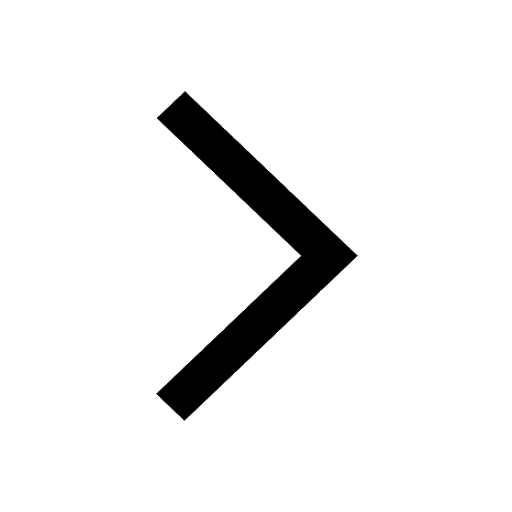
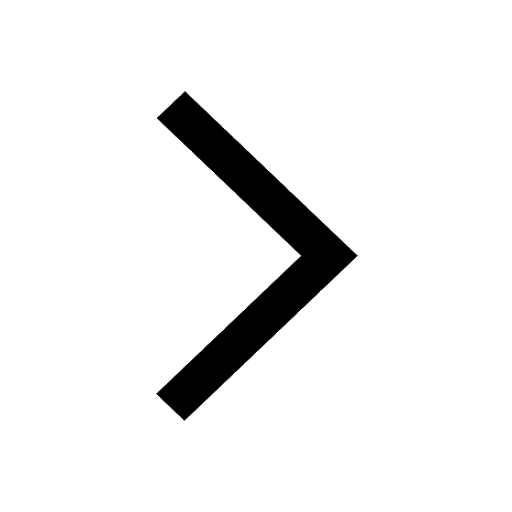
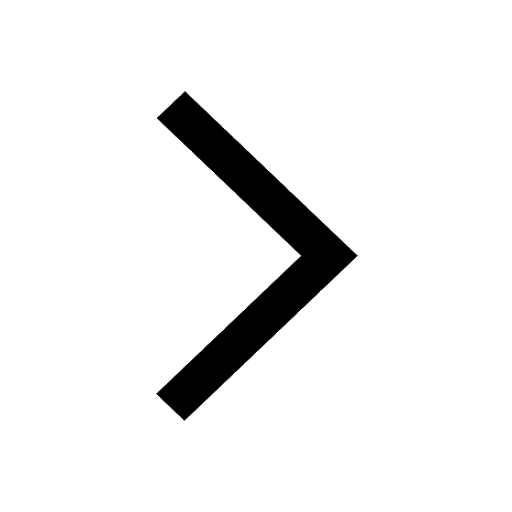
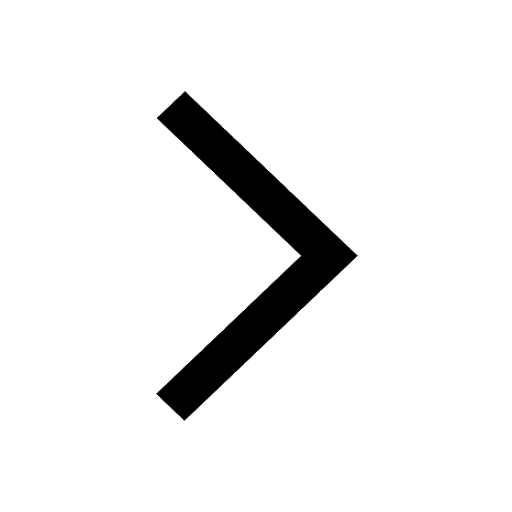
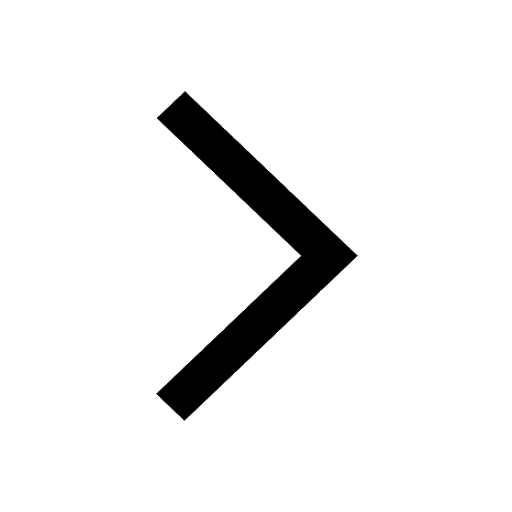
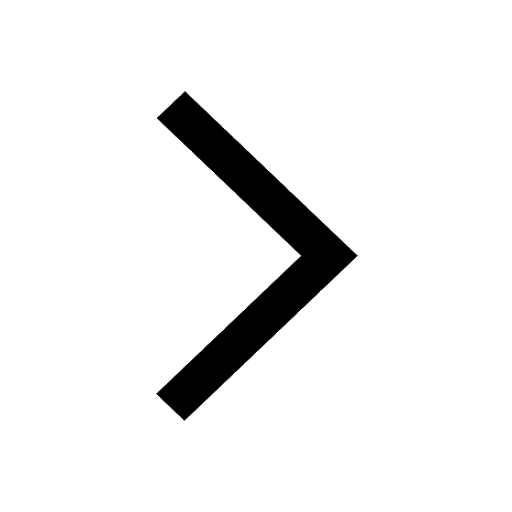
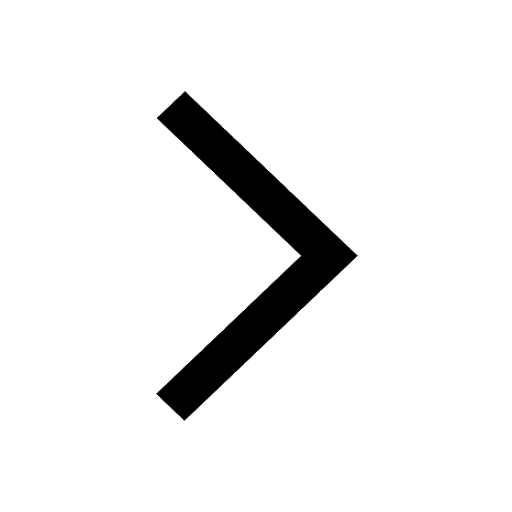
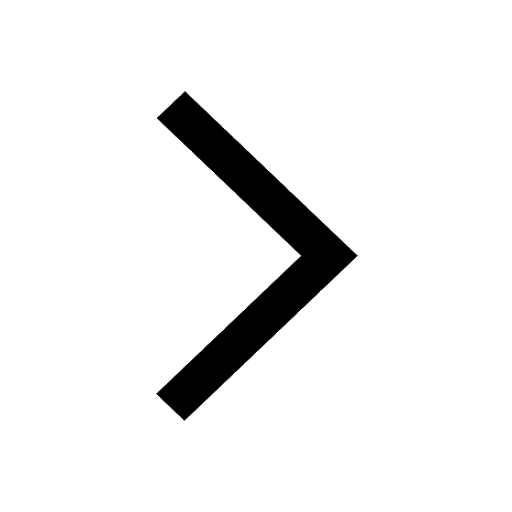
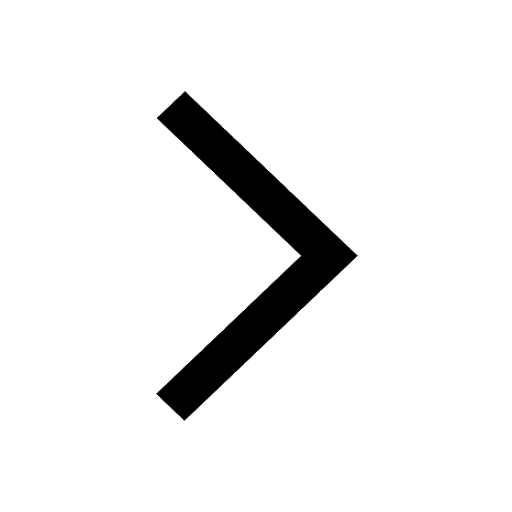
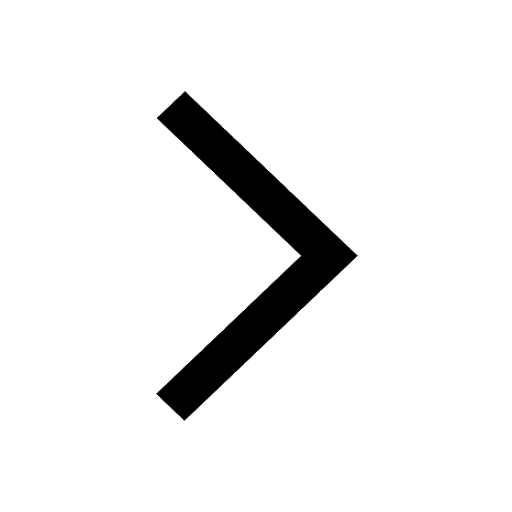
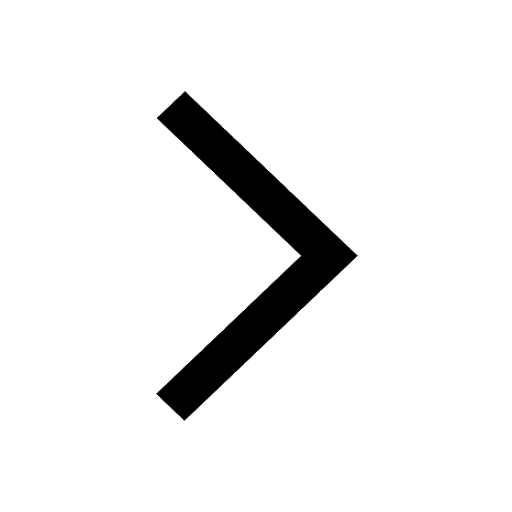
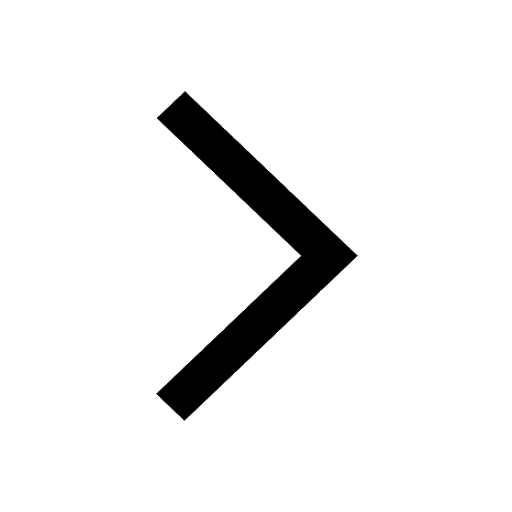