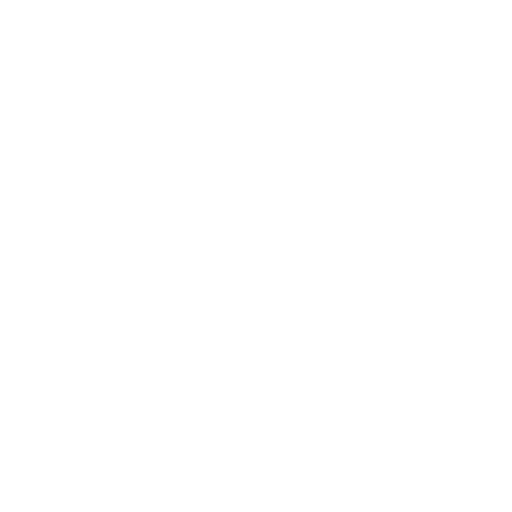

Yield Strength vs Tensile Strength: Key Differences and Stress-Strain Graph
In Physics, the concept of yield strength forms the foundation for understanding how materials respond when subjected to external forces. Yield strength specifies the maximum amount of stress that can be applied to a material, such as steel or aluminum, before it starts to deform permanently. Up until the yield point, the material behaves elastically — meaning it can stretch and return to its original shape when the stress is removed.
Once the stress on the material crosses the yield strength, however, the material will not snap back to its original form, leading to permanent changes in shape. This is crucial for assessing safety and usability in structures and machinery. Knowing yield strength also helps engineers select materials that can withstand required loads in bridges, automotive components, aerospace parts, and more.
What is Yield Strength?
Yield strength represents the stress level at which a material transitions from elastic behavior (temporary, reversible deformation) to plastic behavior (permanent deformation). For example, if you bend a plastic ruler slightly, it will straighten back out. But beyond a certain bend, the ruler either snaps or stays permanently bent—this limit is the yield strength.
The concept is key in selecting and testing materials for any place where a little 'give' is necessary, like in suspension bridges that move slightly with wind and traffic. If any part of the material passes its yield strength, it is considered to have failed in terms of its ability to recover its shape.
The term 'proof stress' is often used in this context and typically refers to a specific, often small, permanent deformation occurring — such as 0.2% elongation in a standard test sample.
What is Tensile Strength?
Tensile strength, often called "ultimate tensile strength," describes the greatest amount of stress a material can bear as it is stretched or pulled before it finally breaks apart. It shows the material's ductility, or its ability to be shaped and stretched before breaking.
Materials with high tensile strength play a vital role in aerospace and engineering applications, where intense forces may push a material to its physical limits. The "fracture strength" or "breaking strength" is another term used for tensile strength and marks the point at which the material splits into two.
Typically, yield strength is considered an earlier, safer limit: what force will start to cause permanent change. Tensile strength offers the absolute limit: the maximum pulling force before everything fails.
Key Differences Between Yield Strength and Tensile Strength
Aspect | Yield Strength | Tensile Strength |
---|---|---|
Definition | Maximum stress before permanent shape change | Maximum stress before breaking/separating |
Physical Meaning | Start of irreversible deformation | Breaking, fracturing, or splitting point |
Material State | Still in one piece, but permanently changed | Material separates into two parts |
Applications | Used in structural design limits | Used in determining material failure |
Formula for Yield Strength
The general formula to determine yield strength (σy):
where:
- σy = yield strength (in pascals, Pa or megapascals, MPa)
- Fyield = force at yield point (in newtons, N)
- A = original cross-sectional area (in m2)
This formula helps in practical calculations during lab experiments or while evaluating the safety and performance of real-world structures.
Step-by-Step Approach to Solving Problems
- Measure or identify the cross-sectional area (A) of the material.
- Gradually apply force (F) to the material until it reaches the point where it does not return to its original shape.
- Note the force at the yield point (Fyield).
- Use the formula: σy = Fyield / A
- Express the answer in Pa or MPa for clarity.
Practical Example
Suppose a steel rod with a cross-sectional area of 2 cm2 yields under a force of 40,000 N.
Convert area to m2: 2 cm2 = 2 x 10-4 m2
Yield strength, σy = 40,000 N / 2 x 10-4 m2 = 2 x 108 Pa = 200 MPa
This means the steel rod's yield strength is 200 MPa.
Yield and Tensile Strength as Performance Indicators
Both yield and tensile strength are vital for engineers. They help predict if a bridge, bracket, or satellite part will perform safely when loaded, pressed, or pulled. Yield strength tells engineers the maximum daily operational load without causing permanent change, while tensile strength tells when catastrophic failure or breaking is imminent.
Material/Application | Yield Strength (MPa) |
Tensile Strength (MPa) |
---|---|---|
Mild Steel (common construction use) | ~250 | ~400 |
304 Stainless Steel | ~215 | ~505 |
6061 Aluminium Alloy | ~240 | ~310 |
Application in Real-World Context
Structures such as bridges or building supports are designed so that the stress from regular use stays below the yield strength of their core materials. This ensures they remain safe and recover their shape daily. During heavy impacts or emergencies, exceeding the yield strength can cause permanent change, but exceeding tensile strength will lead to breakage and total loss of function.
In manufacturing, sometimes an item is purposefully bent or formed at the yield point — for example, when producing metal brackets. The knowledge of yield and tensile strengths makes this process accurate and safe.
Related Vedantu Resources & Next Steps
- Mechanical Properties of Solids
- Stress and Strain Mechanics basics
- Elasticity: Concepts and Types
- Tensile Stress and Yield Point practical guides
- For problem-solving sets, visit Stress and Strain Problems
Key Formula/Concept | Description |
---|---|
σy = Fyield / A | Yield strength equals force at yield divided by original area |
Elastic limit | Maximum stress for full shape recovery |
Tensile strength | Maximum stress material can withstand before breaking |
For further clarification and practice, explore Elastic Behavior of Materials or try real-world questions from Elastic Limit and Young’s Modulus topics. Continue experimenting with formulas, solve practice questions, and connect concepts with real-life engineering problems.
FAQs on Yield Strength in Physics: Meaning, Formula, and Applications
1. What is yield strength?
Yield strength is the maximum stress that a material can withstand before it undergoes permanent plastic deformation. Up to the yield point, the material returns to its original shape when the load is removed. Beyond this point, it will not fully recover.
2. What is the yield strength formula?
The standard formula for yield strength (σy) is:
σy = Fyield / A,
where:
- Fyield = Force at yield point (in Newtons)
- A = Original cross-sectional area (in m²)
Yield strength is measured in Pascals (Pa) or Megapascals (MPa).
3. What is 0.2% yield strength (proof stress)?
0.2% yield strength (or proof stress) refers to the stress at which a material undergoes a permanent strain of 0.2%. For materials without a distinct yield point, this method is used to determine yield strength by drawing a line parallel to the elastic region of the stress–strain curve, offset by 0.2% strain.
4. Is yield strength always less than tensile strength?
Yes, yield strength is always lower than tensile (ultimate) strength. The yield strength marks the start of permanent deformation, while tensile strength is the maximum stress a material can endure before breaking.
5. What is the SI unit of yield strength?
The SI unit of yield strength is the Pascal (Pa). In engineering, it is usually expressed in Megapascal (MPa), where 1 MPa = 106 Pa.
6. What is the yield strength of mild steel used in exams?
The standard yield strength of mild steel used in competitive exams is 250 MPa. Always check exam guidelines for specific material values if mentioned.
7. How is yield strength determined on a stress–strain curve?
Yield strength is identified at the point where the stress–strain curve deviates from a straight line (the elastic region). For some materials, it is marked at the 0.2% offset strain as the curve may not show a sharp yield point.
8. How is the 0.2% offset method used to find yield strength?
The 0.2% offset method is commonly used for materials lacking a clear yield point. Steps:
1. Draw the stress–strain curve.
2. Draw a line parallel to the elastic portion, offset by 0.2% strain.
3. The intersection of this line and the curve gives the 0.2% yield strength.
9. What is the difference between yield strength and tensile strength?
Yield strength is the stress at which a material starts permanent deformation, while tensile strength (ultimate strength) is the maximum stress the material can withstand before fracture.
- Yield strength < Tensile strength
- Yield strength relates to plastic deformation; tensile strength relates to failure.
10. Why is yield strength important in engineering design?
Yield strength ensures that structures and components remain within safe limits of elastic behavior under applied loads. Designing below the yield strength helps prevent permanent deformation and promotes durability in engineering applications such as buildings, bridges, and machinery.
11. What are the typical yield strength values for common materials?
Typical yield strength values (in MPa):
- Mild Steel: 250
- 304 Stainless Steel: 215
- 316 Stainless Steel: 290
- 6061 Aluminium Alloy: 240
Always refer to official sources or exam guidelines for precise values.
12. Can yield strength vary between alloys of the same base metal?
Yes, yield strength can vary significantly between different alloys of the same base metal due to differences in composition, heat treatment, and processing methods. Always use data relevant to the specific alloy in question.
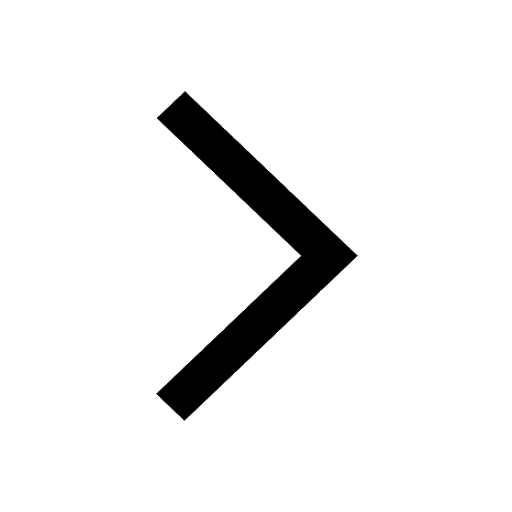
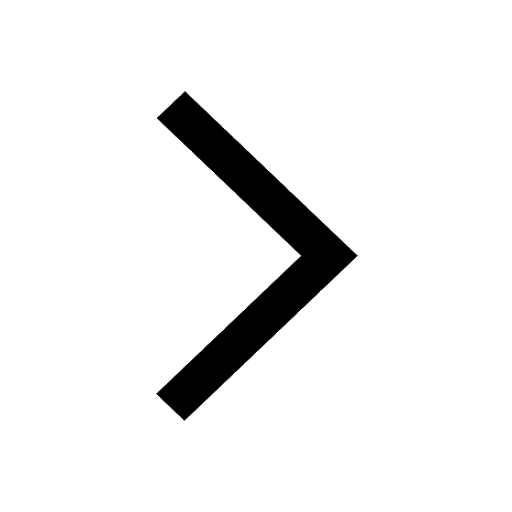
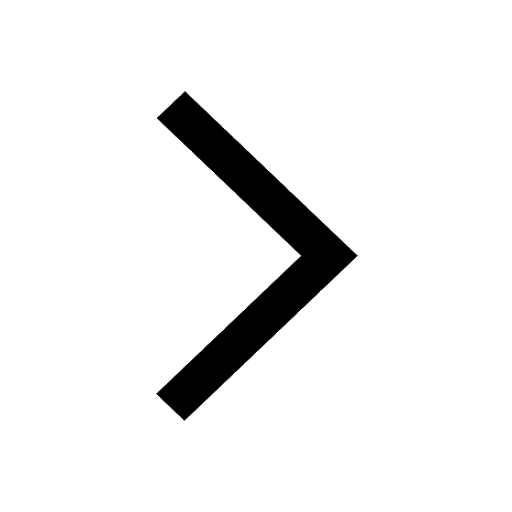
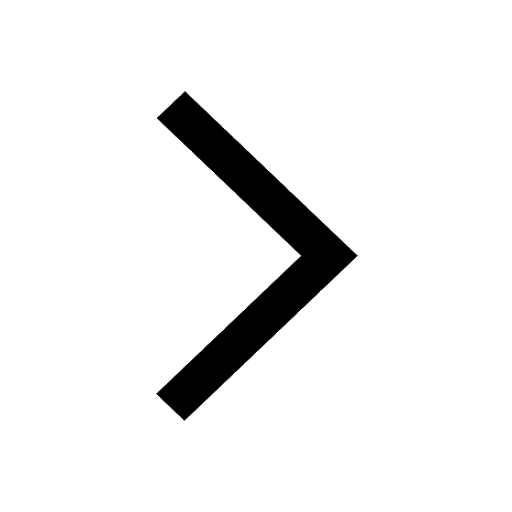
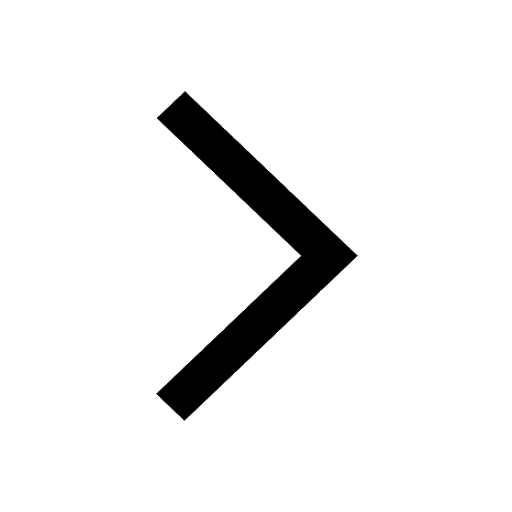
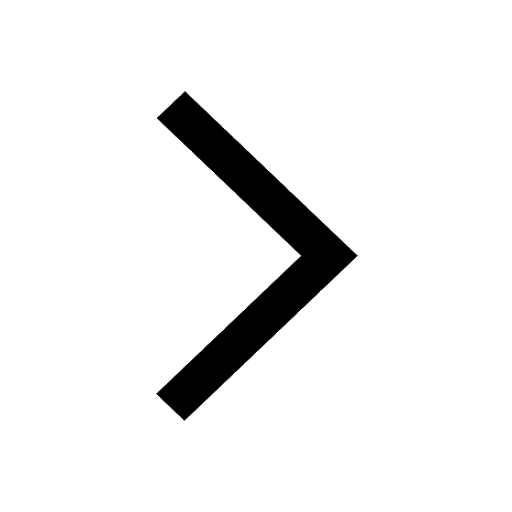
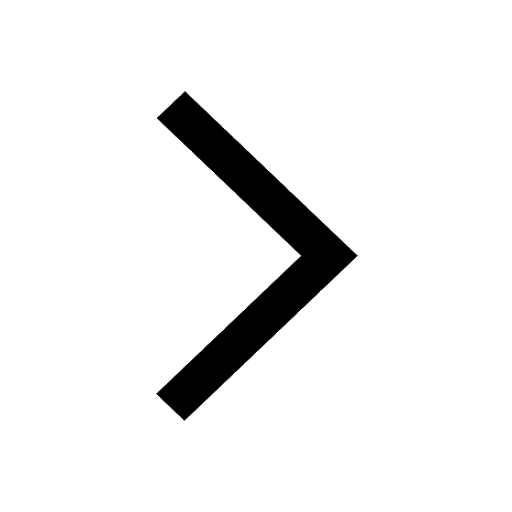
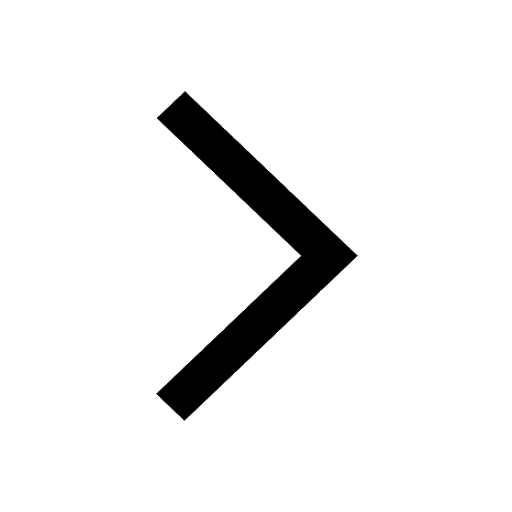
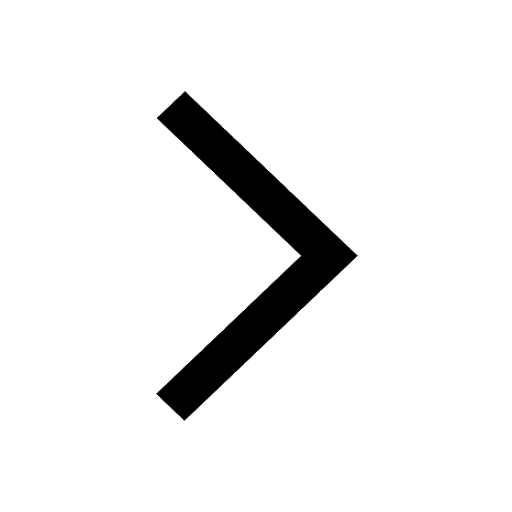
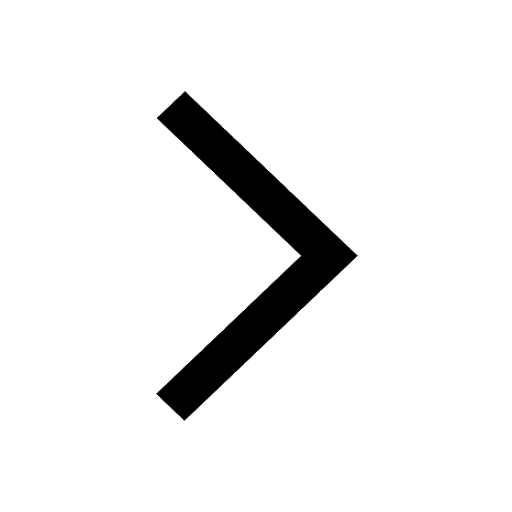
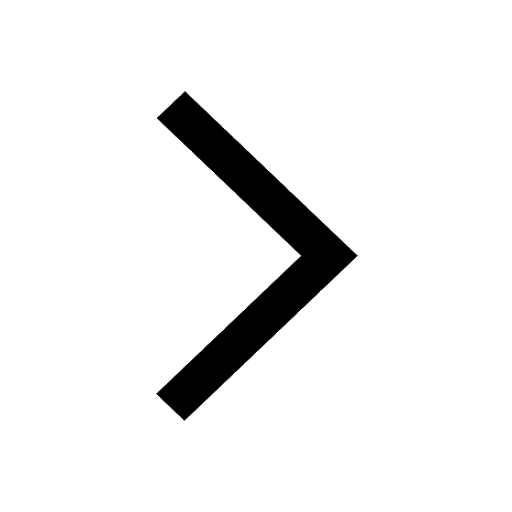
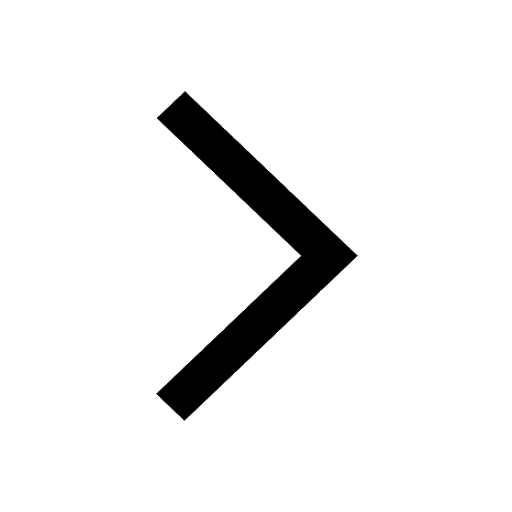
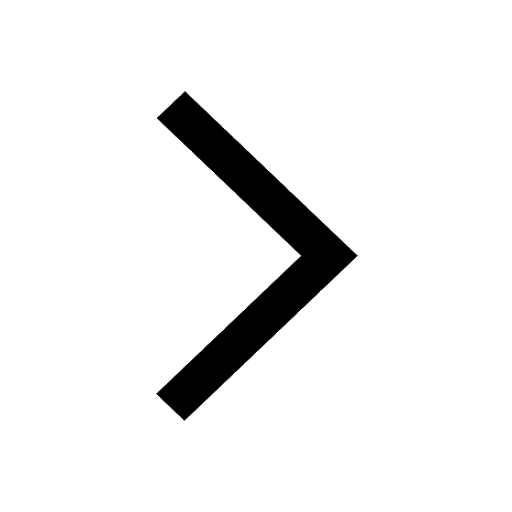
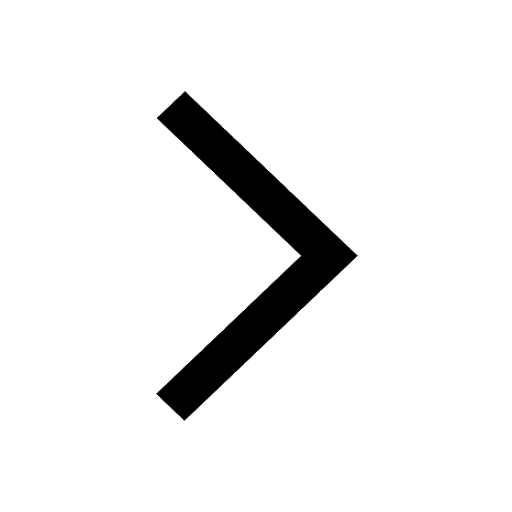
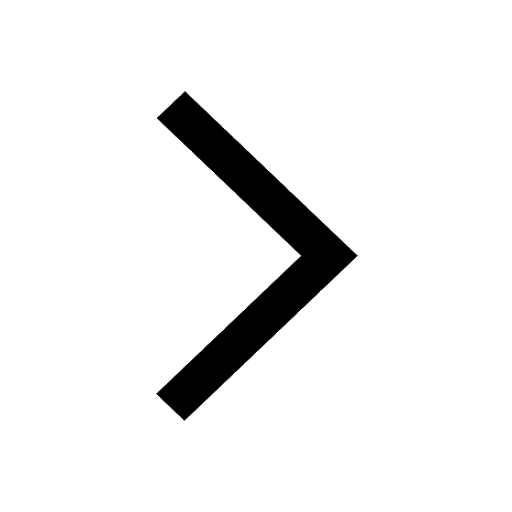
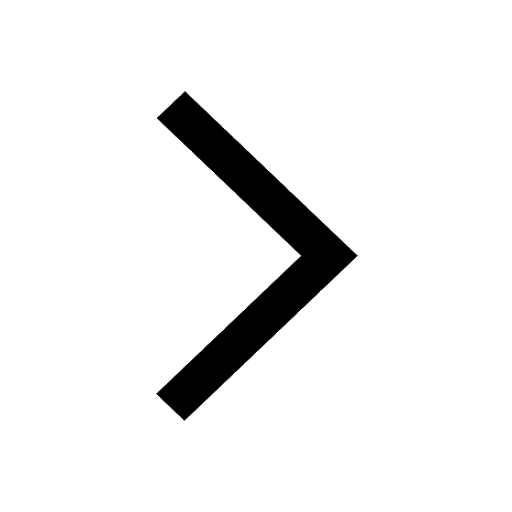
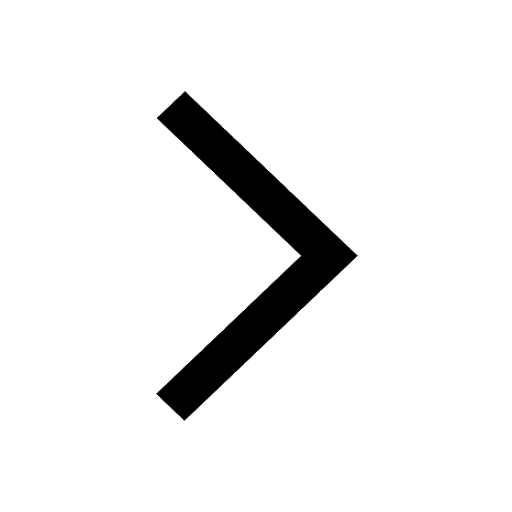
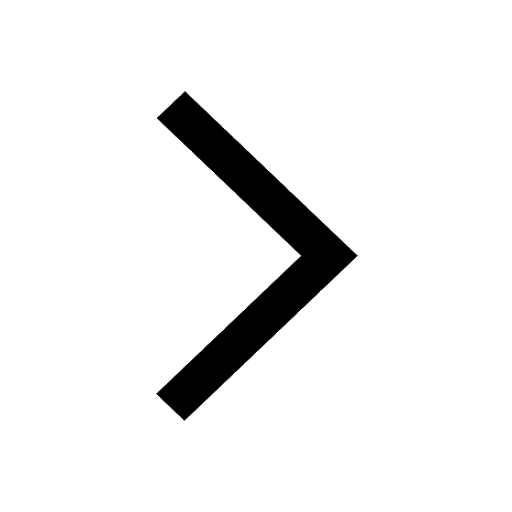