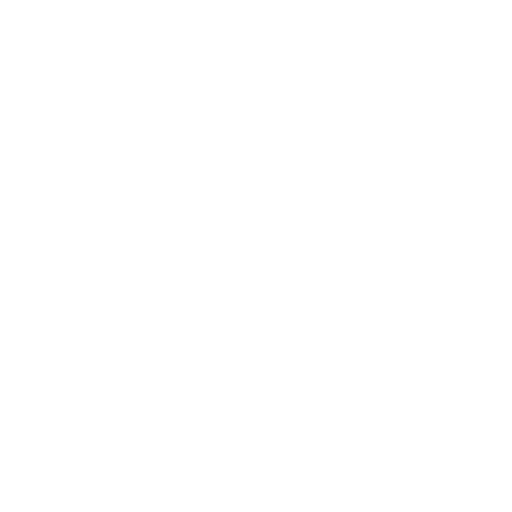

How Does Solid Deformation Affect Materials in Physics?
Matter has three forms: solids, liquids, and gases. They differ in the way ions, molecules, and atoms are arranged in them. Solid is characterized by tightly packed particles that are not free to move around within the substance. A solid can change its shape when pressure is applied to it. The change might be very little for some structures like a building or very large in objects like a spring. This article will look into what is deformation and what are the different types of deformation that can happen in a solid. Let us first define deformation.
Deformation Definition
What forces act on a solid object affects the spacing of atoms within the solid to a small extent. This change in spacing changes the external structure or shape and size of the solid, and it is termed as deformation of solids.
Stress and Its Types
Stress is considered as a force that produces strain when it acts on an object or material. The unit of stress is force/area (for example, lb/in2) since the stress is applied over an area. The pressure is a special type of stress where forces are acting in equal magnitude from all directions. But if the force from all directions is not equal, then we get differential stress. There are mainly three types of stress:
Tensile Stress
This is also called extensional stress, which causes the material (to which stress is applied) to stretch. An example is the stretching of a rubber band.
Compressive Stress
This kind of stress results in the object being squeezed or squashed. An example is when you squeeze a ball; you are applying compressive stress.
Shear Stress
The deforming stress acts tangentially to the object's surface and the result in either slippage or translation of the object.
[Image will be Uploaded Soon]
Features of Deformation in Solids
When stress is applied to a solid, a deformation occurs, which gives rise to internal intermolecular forces in the solid that oppose the forces being applied.
If the applied forces are not so strong, then the internal molecular forces can resist the stress, and the object can acquire a new equilibrium state. Once the load is removed, the object then comes back to its original state.
If the force is very large, there could be permanent deformation of solids or even a complete structural failure.
The type of deformation that a solid undergoes depends on its material, size, geometry, and forces.
Types of Deformation of Solids
A strain is defined as a change in the size, shape, or volume of an object. Strain could also be in the form of any movement of the material, including titling and translation.
Solids can undergo various types of deformation as described below:
Elastic deformation - This kind of deformation is reversible, and the object returns to its original size and shape once the applied force is removed.
Linear elastic deformation is given by Hooke’s law that states that the amount a body extends is directly proportional to the force applied on it provided the elastic limit of the object is not exceeded. The deformation formula according to Hooke’s law is; σ = E * ε, where σ is the force applied, E is the spring or elastic constant (called young’s modulus), and ε is the extension or resulting strain.
The elastic constant is measured as force per unit extension, and its unit is N m-1. It is denoted by the gradient of the graph drawn by force against the extension.
When the material reaches its yield strength, its elastic range ends, and plastic deformation begins.
Stress = Force/cross-sectional area
[Image will be Uploaded Soon]
Plastic or ductile deformation - This is an irreversible kind of deformation that starts as elastic deformation, and the object can partially return to its original state till this stage. A material like soft thermoplastic has a large plastic deformation range. Some ductile metals like gold, silver, and copper also have a large range of plastic deformation. Materials with minimal plastic deformation ranges are rubber, hard, thermosetting plastics, and ceramics. Plastic deformation can be of different types under tensile stress:
Strain hardening region - Due to the movement of atoms, the material becomes harder.
Necking region - After the ultimate strength is reached, there is a reduction in the cross-sectional area of the specimen. At this point, the material can no longer tolerate the maximum stress, and there is a rapid increase in the strain in the object.
Fracture - This indicates the end of plastic deformation where the material breaks.
[Image will be Uploaded Soon]
Young’s Modulus
Young’s modulus is a fundamental property of all materials which is unchangeable. However, it is dependent on pressure and temperature. Young’s modulus is also called the elastic modulus, and in simple words, it describes the stiffness of the material, i.e., how easily you can bend or stretch the material. The name “Young’s modulus” comes from 18th-century English physicist and physician Thomas Young. Young’s modulus describes the elastic properties of a material undergoing compression or tension in only one direction. It indicates a material’s ability to withstand length changes when it is undergoing lengthwise compression or tension. Mathematically it is expressed as:
Young’s modulus = stress/strain = (F * L0)/(A * (Ln - L0))
Or, F/A = Y * (ΔL/L0)
[Image will be Uploaded Soon]
Where L0 is the original length, Ln is the new length, F is the force applied, and A is the cross-sectional area of the metal bar.
Young’s modulus is measured in pascal and 1 Pascal = Nm-2
FAQs on Solid Deformation: Definition, Types & Examples
1. What is meant by the deformation of solids in Physics?
In physics, the deformation of a solid refers to any change in its size or shape when an external force is applied. This change is quantified by strain, which is the relative change in dimension. The internal restoring force per unit area that develops within the solid to oppose this external force is known as stress. Every solid material deforms to some extent when a load is applied.
2. What is the difference between elastic and plastic deformation?
The key difference lies in the material's ability to return to its original state after the force is removed.
- Elastic Deformation: This is a temporary and reversible change. The solid returns completely to its original shape and size once the external force is removed. This occurs as long as the force is within the material's elastic limit.
- Plastic Deformation: This is a permanent and irreversible change. If the applied force exceeds the elastic limit, the solid does not fully regain its original shape, and a permanent change remains even after the force is removed.
3. What are the main types of stress and strain a solid can experience?
Stress and the resulting strain are classified based on the direction of the applied force. The main types are:
- Tensile Stress & Longitudinal Strain: Occurs when a force pulls on a solid, causing it to stretch or elongate.
- Compressive Stress & Longitudinal Strain: Occurs when a force pushes on or squeezes a solid, causing it to shorten.
- Shear Stress & Shearing Strain: Occurs when a force acts tangentially to a surface, causing one layer of the solid to slide over another, changing its shape without changing its volume.
4. What is Hooke's Law and what is its significance in solid deformation?
Hooke's Law is a fundamental principle that describes elastic behavior. It states that, within the elastic limit, the stress applied to a solid is directly proportional to the strain produced. Mathematically, it is expressed as:
Stress ∝ Strain, or Stress = E × Strain.
Here, 'E' is the constant of proportionality known as the Modulus of Elasticity (e.g., Young's Modulus). Its significance is that it defines the predictable, linear relationship between force and deformation for most materials under small loads, which is crucial for engineering design.
5. How does a stress-strain curve help in understanding the key properties of a material?
A stress-strain curve is a graphical representation of a material's behaviour under load and provides critical information about its mechanical properties. By analysing the curve, we can determine:
- Elasticity: The initial linear slope indicates the Modulus of Elasticity (stiffness).
- Yield Strength: The point where the material begins to deform plastically.
- Ultimate Tensile Strength (UTS): The maximum stress the material can withstand before it starts to neck down and weaken.
- Ductility/Brittleness: The amount of plastic deformation the material can endure before it fractures. A long plastic region indicates a ductile material, while a short one indicates a brittle material.
- Fracture Point: The point at which the material breaks.
6. Why is it crucial for engineers to consider both Young's Modulus and Poisson's ratio when designing structures?
Engineers must consider both to ensure structural integrity and safety. Young's Modulus (E) measures a material's stiffness, or its resistance to changing length under tension or compression. This helps predict how much a beam will sag or a column will compress under a specific load. However, materials don't just change length; they also change in their transverse (sideways) dimensions. Poisson's Ratio (ν) quantifies this effect. For instance, when a rod is stretched, it becomes thinner. Understanding this ratio is vital for designing components that fit together precisely and for predicting failure modes where multidimensional stresses are involved, like in pressure vessels or complex machine parts.
7. What happens at a microscopic level inside a solid during elastic versus plastic deformation?
The behaviour at the microscopic level is fundamentally different:
- During elastic deformation, the external force stretches the interatomic bonds between the atoms in the material's crystal lattice. The atoms are displaced from their equilibrium positions but do not break their bonds. When the force is removed, these bonds pull the atoms back to their original positions.
- During plastic deformation, the applied force is strong enough to cause planes of atoms to slip past one another. This involves the movement of defects in the crystal structure called dislocations. Since the atoms move to new, stable positions, the change is permanent, and the material does not return to its original shape.
8. What is the main difference between a ductile and a brittle material?
The main difference is their behaviour after the elastic limit is crossed. Ductile materials, such as copper and aluminium, can undergo significant plastic deformation before they fracture. They show a clear 'necking' process where they thin out before breaking. In contrast, brittle materials, like glass or cast iron, show very little or no plastic deformation. They fracture suddenly without any significant change in shape as soon as the stress exceeds their ultimate strength.
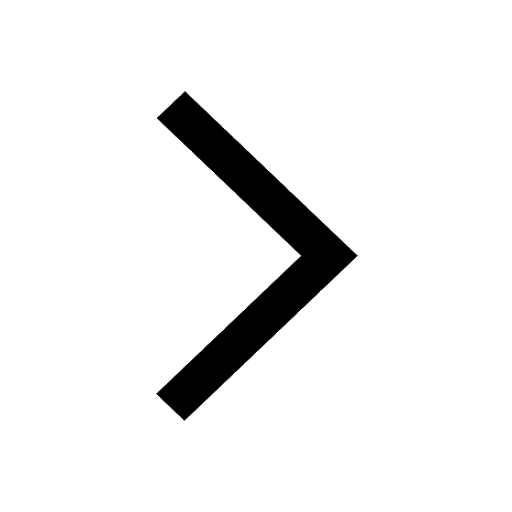
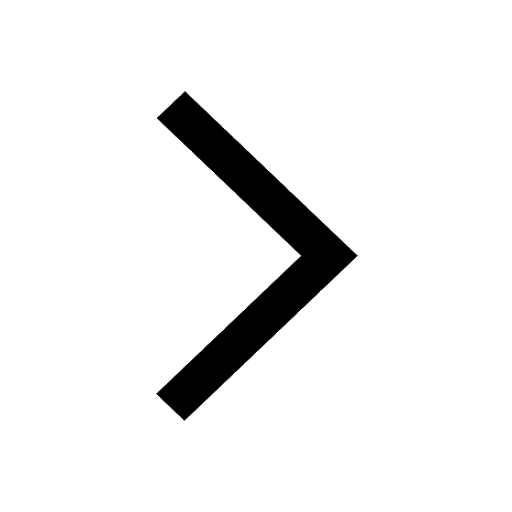
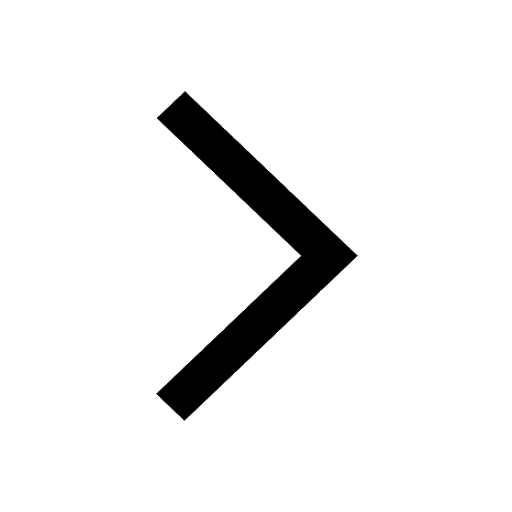
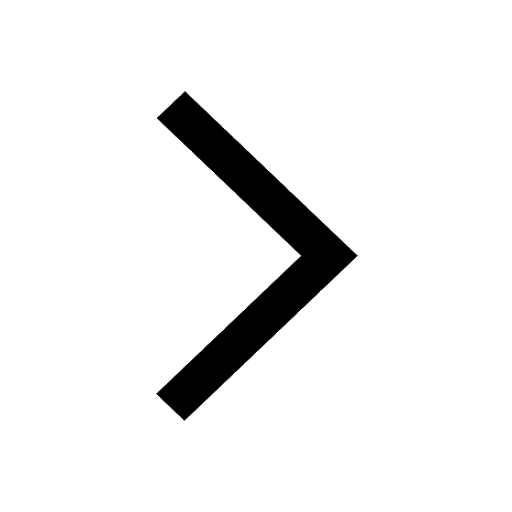
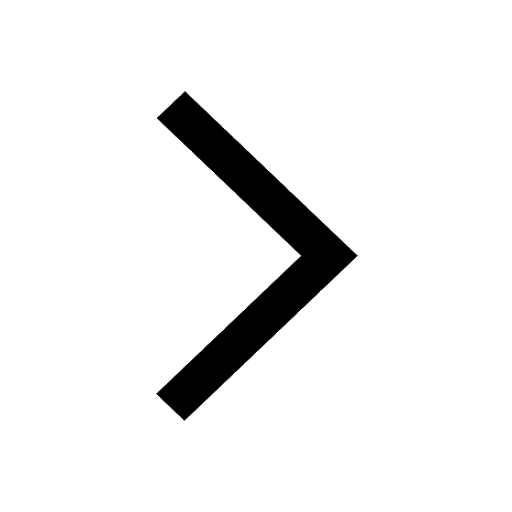
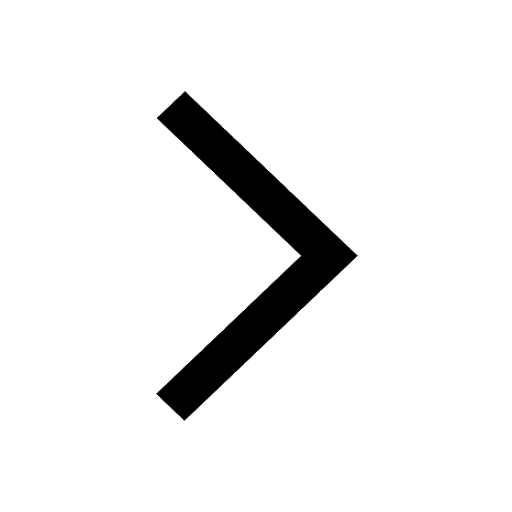
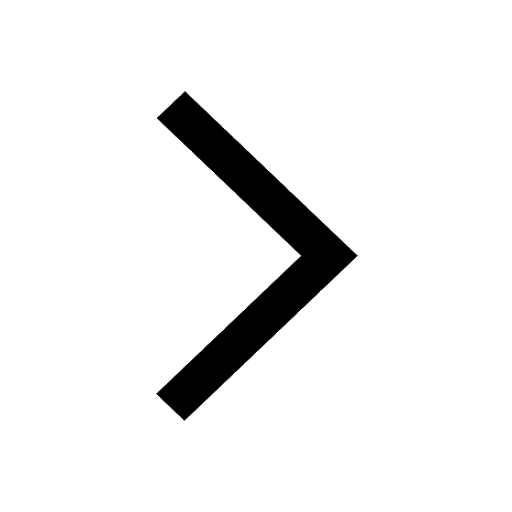
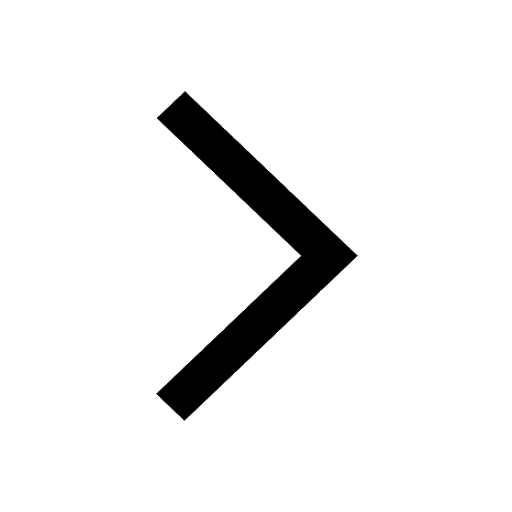
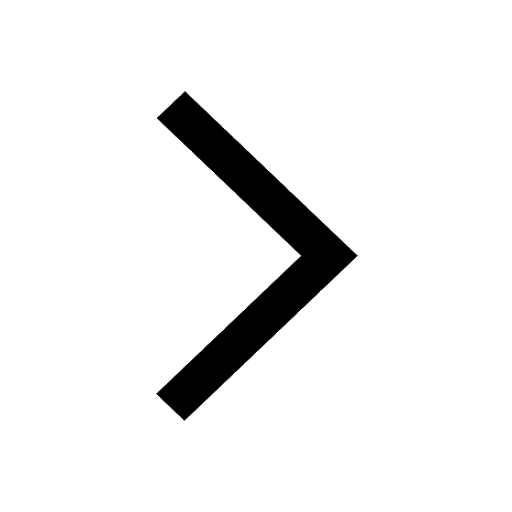
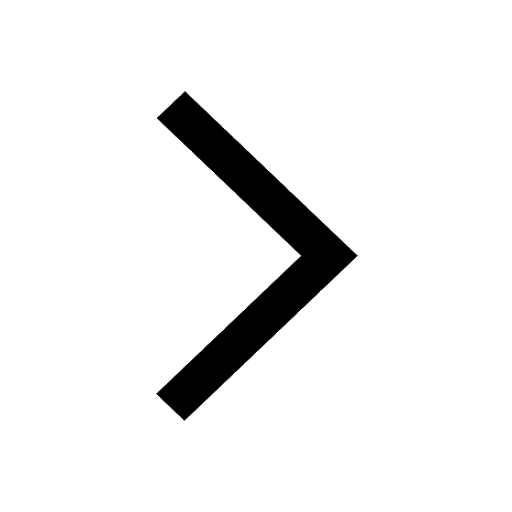
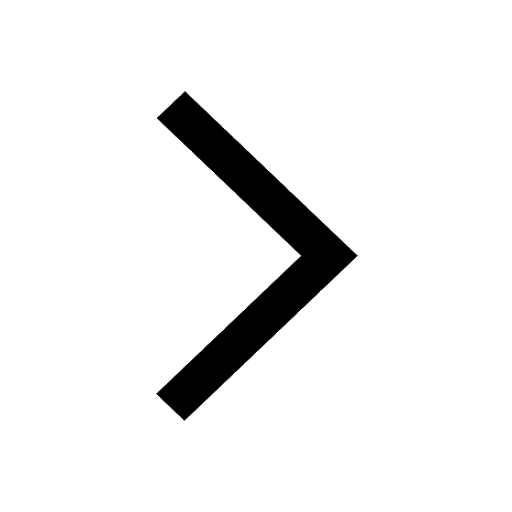
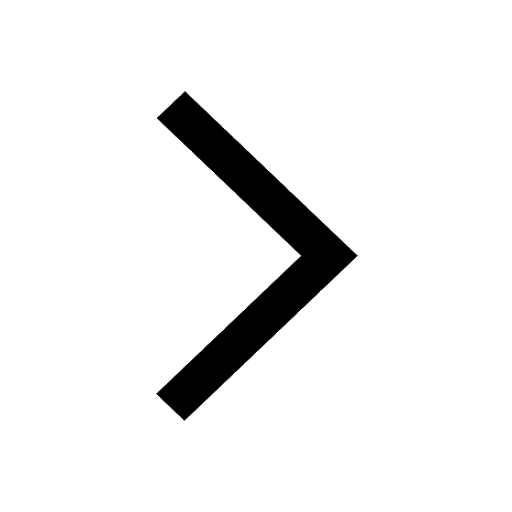
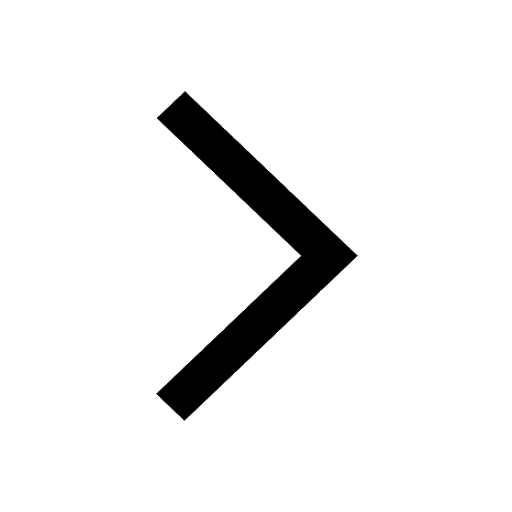
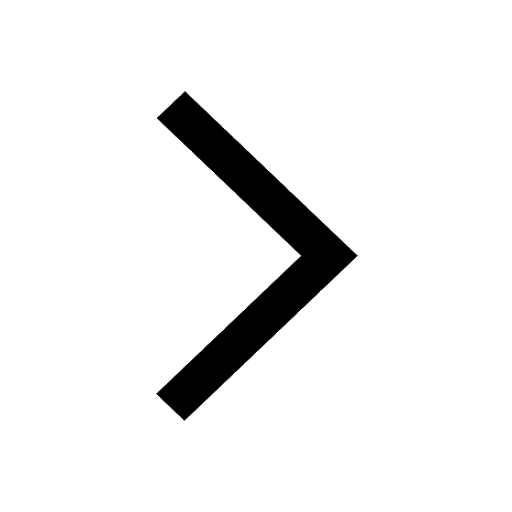
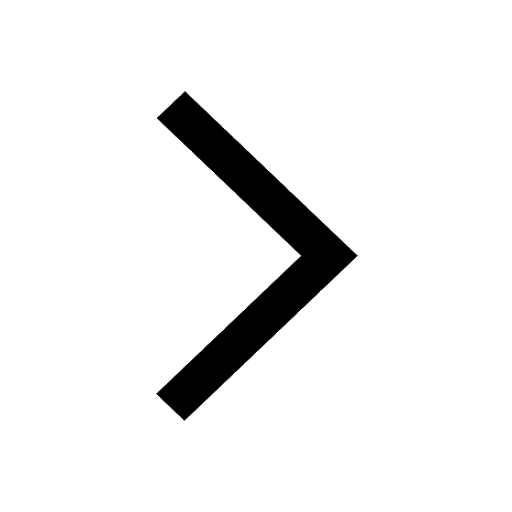
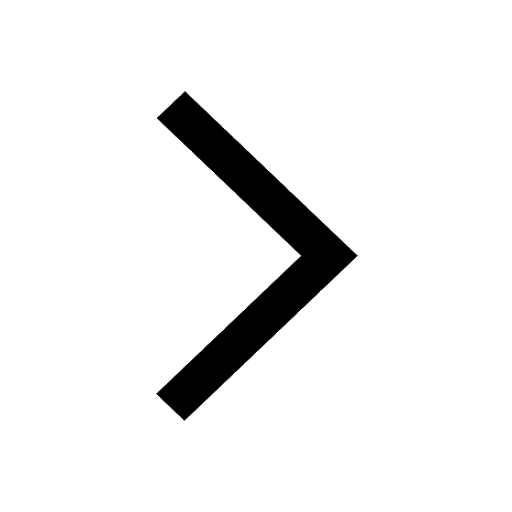
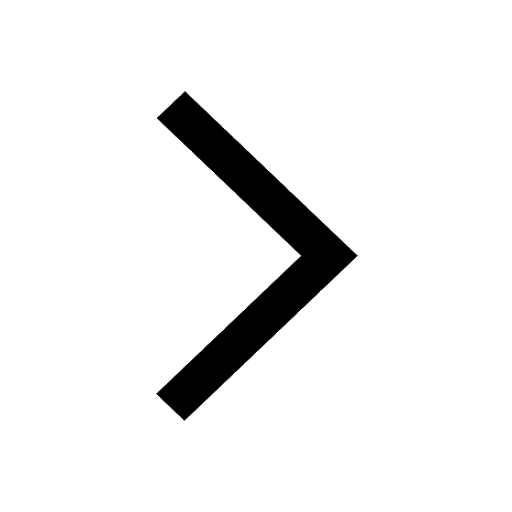
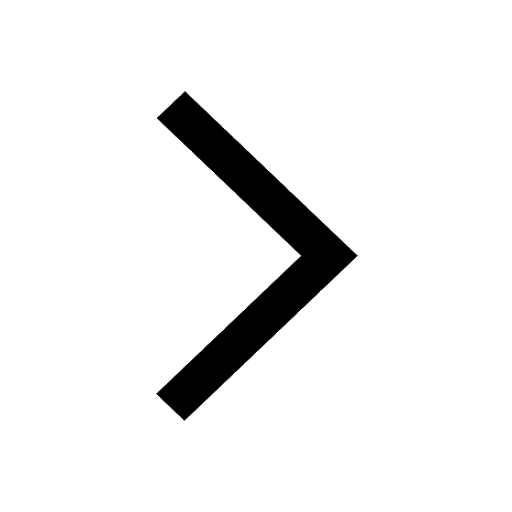