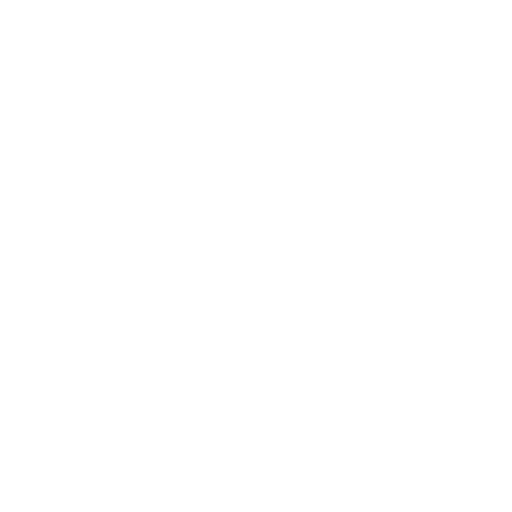

How Electroplating Works: Benefits and Everyday Applications
The term 'Electroplating' refers to the process of coating a metal with another metal by the process of hydrolysis.
The part that is to be coated, behaves as the negative charge which is the cathode of an electrolytic cell. The solution of the salt’s metal which has to be coated is electrolyte.
Hydrolysis is a chemical reaction in which a molecule of water breaks one or more chemical bonds. Metals are electroplated mostly for decorative purposes or for preventing the corrosion of metals. In electroplating, an electric current is used for reducing the dissolved metal cations (positively charged ions) at the cathode (negatively charged electrode) to have a lean coherent metal coating on the electrode. The process is quite often applied in the electrical oxidation of anions (negatively charged ions) on a solid substrate, for instance - in the formation of silver chloride (AgCl3) on the silver wire to form silver chloride electrodes.
Electroplating is primarily used to modify or enhance the surface features of an object for the prevention of corrosion or abrasion. However, the process can also be extensively used to make objects by electroforming or building their thickness.
(Image will be Uploaded Soon)
Working Concept of Electroplating
For having a better understanding of the process of electroplating, let us consider the example of a gold coating. In this particular scenario, we will enhance the appearance of metallic jewellery by electrodepositing a layer of gold on it. We will begin by connecting the gold plating to the anode, which is the positively charged electrode, and the jewellery to the cathode, which is the negatively charged electrode. Next, we have to immerse both of them in a highly developed electrolytic solution. During this phase, we will supply a DC voltage (direct current) to the anode, so that the gold atoms are oxidized and further get dissolved into the solution. The dissolved ions are then reduced at the cathode and consequently plated on the jewellery. Several factors influence the process of electroplating, namely, the voltage level of the DC, the chemical composition and temperature of the solution, the distance between the anode and the cathode, and the current length of time.
(Image will be Uploaded Soon)
Strike
A strike also known as a flash, which is a special plating deposit that is used as a very thin plating which is high in quality and good adherence. This works as a foundation for the process of plating. A strike uses a current density which is high and a bath with an ion concentration which is low.
It is a slow process, so all the plating processes which are more efficient are used only when the desired thickness of the strike is obtained.
For the combination with the plating of different plating, a striking method is used.
Deposition of Electrochemical
From the late 1990s, in order to manufacture conductive wires of copper in semiconductor devices that are advanced, electrochemical deposition has been used widely.
The methods which are used previously for making aluminium conductive wires into chips through engraving the metal lines and then fill in an insulating film that has chemical Vapor deposition along with physical Vapor deposition processes, were not working with copper because of the hardness of the metal, to solve this problem, this technology was created.
Applications and Uses of Electroplating
One of the prime uses of electroplating is to coat the surface of an object with a thin layer of metal by using the electrochemical process. Besides, electroplating has a plethora of other applications in many industries. A few practical applications and uses of this process are as follows:
Aesthetics
It is a matter of fact that yes - some metals are way more expensive, rare, and valuable than the others, like silver and gold being the most obvious examples. Through the process of electroplating, an extremely thin layer of gold or silver can be used to coat a less valuable metal so that the final product has all the beauty and lustre at a minimal cost. Electroplating, being one of the widely implemented applications today, is extensively used for designing jewellery and other ornaments. Moreover, thin layers of chromium are also used on automobiles and appliances to give them an attractive and shiny appearance.
Commercial Applications
Electroplating is also used on car parts to give a smooth appearance and texture with the help of a thin layer of chromium. As the car owner's request, electroplating can also be done on various other appliances as well.
Prevention of Corrosion
As some metals are more prone to natural processes such as corrosion (conversion of a metal into a chemically stabilized form like oxide, hydroxide, or sulfide), electroplating protects their surface by covering them with a thin layer of metal, which shall be corrosion resistant. Copper, chromium, and nickel, which are the non-corrosive metals, are spread over corrosive metals like iron and steel to prevent corrosion.
(Image will be Uploaded Soon)
Conduction of Electricity
Metals like silver and gold are indeed excellent conductors of electricity; however, they are prohibitively expensive. Through the techniques of electroplating, little amounts of these highly conductive and precious metals can be incorporated into the integrated circuits and electrical components like computers, cell phones, amongst many others, to help in the conduction of electricity.
Reduces Friction
Electroplating can reduce the built-up friction of some materials such as the electrical connectors to a great extent by introducing a certain kind of metal plating on them. For instance - nickel plating improves performance and reduces friction and wear and tear.
Protection from Radiation
Electroplating also helps to protect the materials from various other natural phenomena, including radiation and abrasion, simply by imparting the desired features or characteristics to the surface of the metals, which in general, lack them.
FAQs on Uses of Electroplating Explained with Real-Life Examples
1. What is electroplating, and what is the basic principle behind it?
Electroplating is a process where a thin layer of one metal is coated onto the surface of another metal object. The basic principle is electrolysis. It involves passing a direct electric current (DC) through a solution called an electrolyte, which contains dissolved ions of the coating metal. The object to be plated acts as the cathode (negative electrode), and the metal used for coating acts as the anode (positive electrode). The electric current causes the metal ions from the electrolyte to deposit onto the cathode, forming a smooth, thin layer.
2. What are the primary uses of electroplating in various industries?
Electroplating has several crucial industrial applications, primarily to enhance the properties of a base material. The main uses include:
- Corrosion Prevention: Coating metals like iron with non-corrosive metals like zinc or chromium to prevent rusting.
- Aesthetic Enhancement: Applying a layer of precious metals like gold or silver on cheaper metals to make decorative items and jewellery look attractive.
- Improving Hardness and Durability: Coating tools and machine parts with chromium to increase their resistance to wear and tear.
- Enhancing Electrical Conductivity: Plating electronic components with gold or silver to improve conductivity and ensure reliable performance.
3. Could you give some common real-life examples of electroplated objects?
We encounter many electroplated objects in our daily lives. Some common examples include:
- Kitchen and Bathroom Fittings: Taps, showerheads, and towel racks are often electroplated with chromium for a shiny finish and to prevent corrosion.
- Vehicle Parts: Car bumpers, wheel rims, and bicycle handlebars are coated with chromium for protection and a decorative look.
- Artificial Jewellery: Ornaments made from less expensive metals are electroplated with gold or silver to give them a premium appearance.
- Food Cans: Tin cans used for storing food are made of steel electroplated with a thin layer of tin, which is less reactive and prevents the food from coming into contact with the steel.
- Cutlery: Spoons and forks are often electroplated with silver (EPNS - Electroplated Nickel Silver) for a better look and feel.
4. How does electroplating change the properties of a material?
Electroplating fundamentally alters the surface properties of an object. It can induce changes in three main ways:
- Physical Properties: The most noticeable change is in the object's appearance, improving its lustre, colour, and finish.
- Chemical Properties: It significantly enhances corrosion and chemical resistance, as the outer layer of metal acts as a protective barrier against environmental factors like moisture and air.
- Mechanical Properties: The process can increase the surface hardness, tensile strength, and wear resistance of the object, making it more durable and reducing friction between moving parts.
5. Why is the choice of electrolyte so important in the electroplating process?
The choice of electrolyte is critical because it is the source of the metal ions that form the coating. An effective electrolyte must contain a soluble salt of the coating metal. The concentration and composition of the electrolyte directly influence the quality of the plating, including its brightness, thickness, and how well it adheres to the object. An incorrect or poorly prepared electrolyte can lead to a rough, uneven, or brittle coating that easily flakes off, defeating the purpose of the process.
6. Can non-metallic objects like plastic be electroplated? If so, how is it achieved?
Yes, non-metallic objects like plastic can be electroplated, but not directly, as they do not conduct electricity. The process involves multiple steps. First, the plastic surface is chemically etched to make it rough, allowing the coating to stick better. Then, a thin conductive layer, often of copper or nickel, is deposited onto the surface using a chemical process called electroless plating. Once the plastic object has this conductive layer, it can be treated like a metal object and electroplated using the standard electrolytic method to add further layers of metals like chromium or nickel.
7. What is the difference between electroplating, galvanising, and painting?
These are all methods for surface protection, but they work differently. Electroplating is a broad term for depositing any metal onto another using electricity for various purposes like decoration or wear resistance. Galvanising is a specific type of coating where iron or steel is coated with zinc to provide sacrificial protection against rust; zinc corrodes first, protecting the iron beneath. Painting is a non-electrolytic process that applies an organic or inorganic coating. While it provides a barrier against corrosion and can be decorative, it does not typically enhance mechanical properties like hardness or conductivity in the way electroplating does.
8. Why are objects electroplated with chromium instead of just being made entirely of chromium?
Objects are electroplated with chromium for both economic and practical reasons. Chromium is a very expensive and brittle metal. Making an entire object, like a tap or a car bumper, out of solid chromium would be incredibly costly and the object would be prone to shattering on impact. By using a cheaper and stronger base metal like steel or brass and applying only a very thin layer of chromium through electroplating, manufacturers can achieve the desired properties—a shiny, corrosion-resistant, and hard surface—without the high cost and structural weakness of using solid chromium.
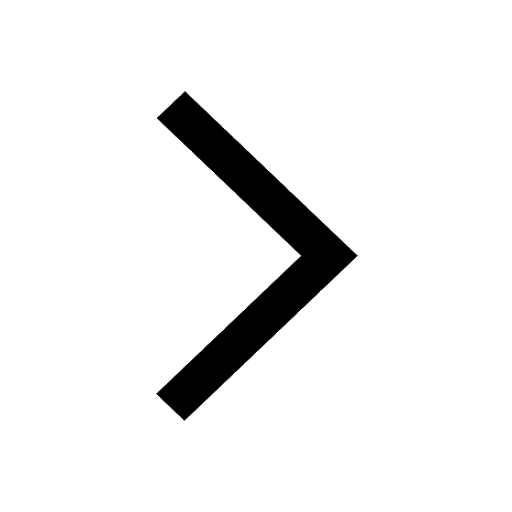
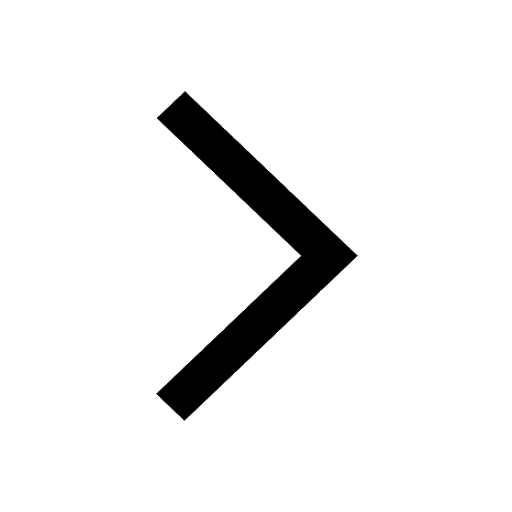
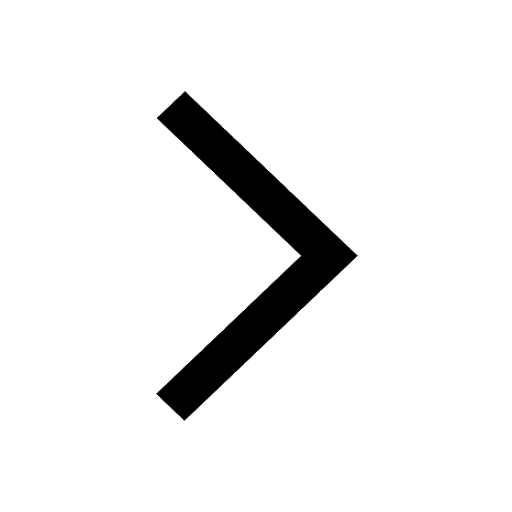
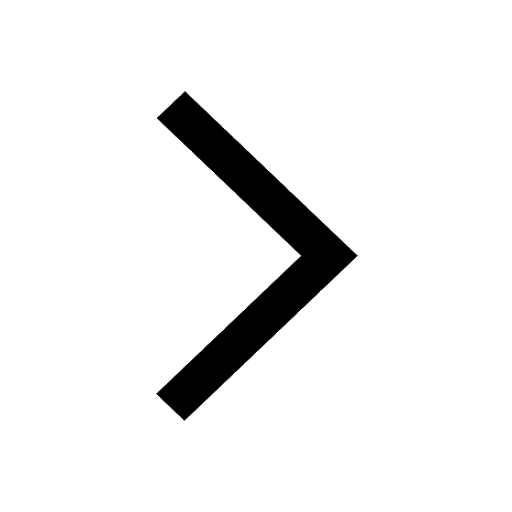
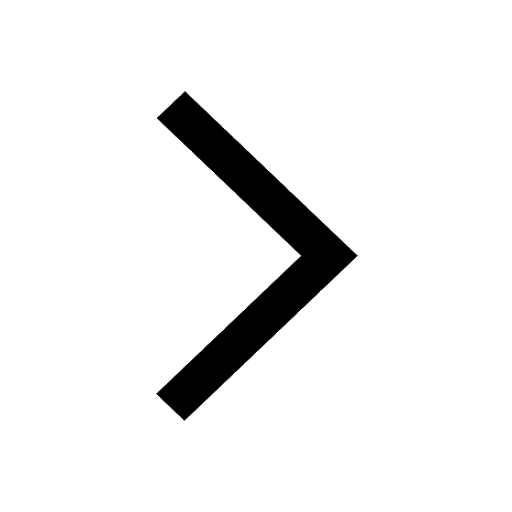
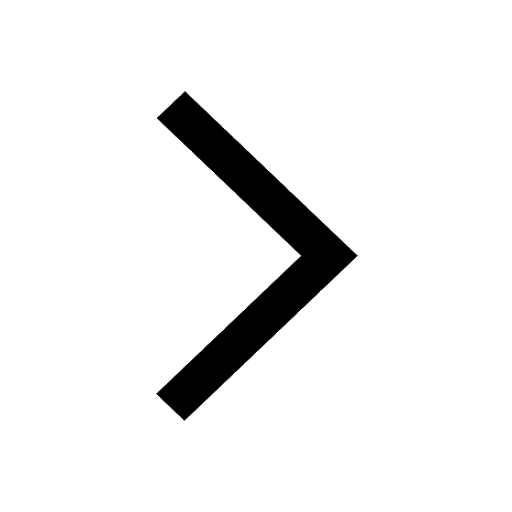