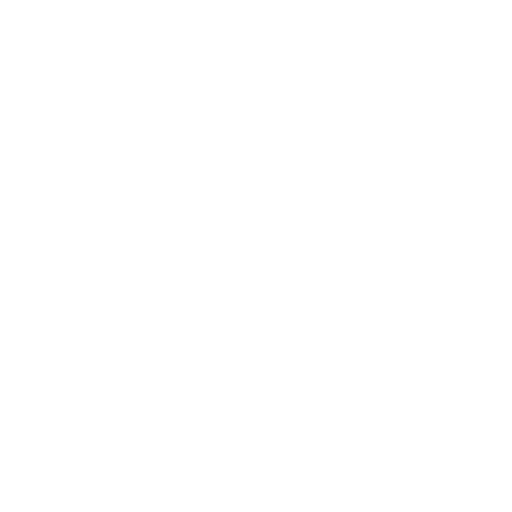

What is Operating Costing?
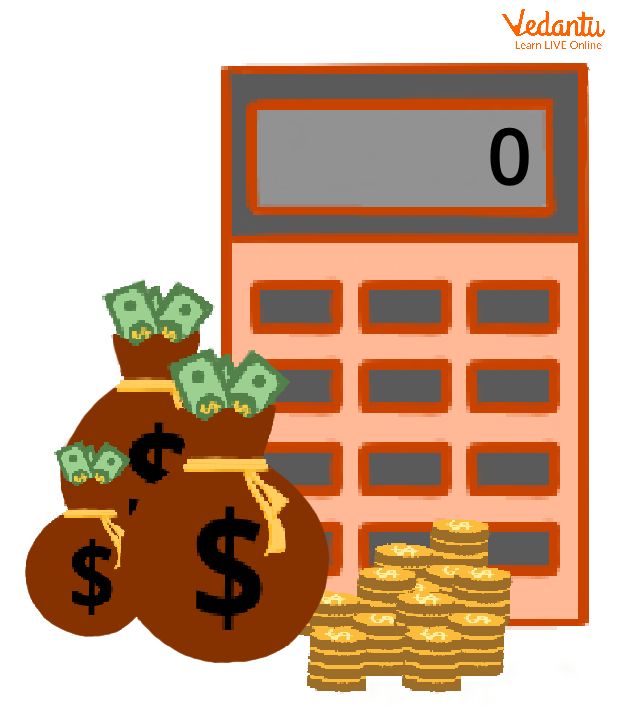
Operation Costing
The operating cost meaning is a technique used to determine a product's final price by analysing the associated overhead costs of a particular production run. This comprises the costs of goods, labour, and facility maintenance. For straightforward production models where items go through the same operating cost formula each time, businesses often employ process costing.
However, some companies could use operation costs to assist with their more complicated production models. For a better understanding of operating costs, let's take an example: a firm selling customised shirts may wish to compute expenses to compensate for varied expenditures.
Why is Operation Costing Important?
Accounting experts can better comprehend and manage expenses thanks to operation costing, which lets organisations account for the total cost of each process. As a result, companies strive to minimise operational expenses while keeping their output as steady and efficient as possible.
This strategy may help businesses increase their profitability by reducing the risk of charging more than necessary for their products because of excessive operating expenditures. In addition, companies that make both mass-produced and custom items may find this approach valuable since it works well in scenarios where products need both specialised and mass-scale manufacturing processes.
How to Calculate Operation Costing?
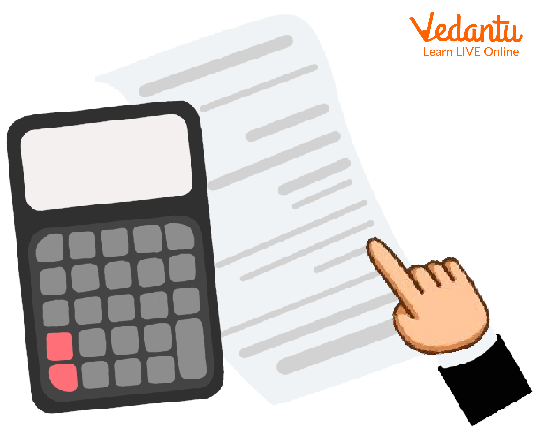
Calculation of Operation Costing
The complexity of a product's manufacturing process might affect how a business determines its production costs, as there are many types of operating costs. It's possible, for instance, that the operating stages of a furniture firm that lets consumers choose their materials, colours, and designs might be more complicated than those of a company that limits clients to a set of predetermined options. Some easy-to-follow guidelines for determining operational costs are listed below:
Cost Analysis of Processes - How much costs to manufacture a product in bulk is the starting point for any analysis of operational expenses. In addition, the sequence in which a business purchases and sells those purchases may significantly impact costs.
Estimate the Project's Price - Step two of gathering operating costs involves tallying up the money spent making a product. Those costs include salaries, supplies, and other similar overheads. Umbrella manufacturers, for instance, have to factor in the price of metals and fabrics, labour hours, rent or lease payments, utilities, and maintenance and repair of machinery and tools.
Determine the Whole Running Expenses - To calculate the total cost of manufacturing, you must first determine how much each task and procedure will cost. You may also keep track of the specifics of any variables or inputs that you believe may change in the future.
Review Sums for Each Procedure - Once you get the summaries, you may evaluate how much the firm spent on each activity. Profit margins, cost factors, and outliers may all help you figure out where your business might stand to improve.
Upsides of Learning about Operational Costs
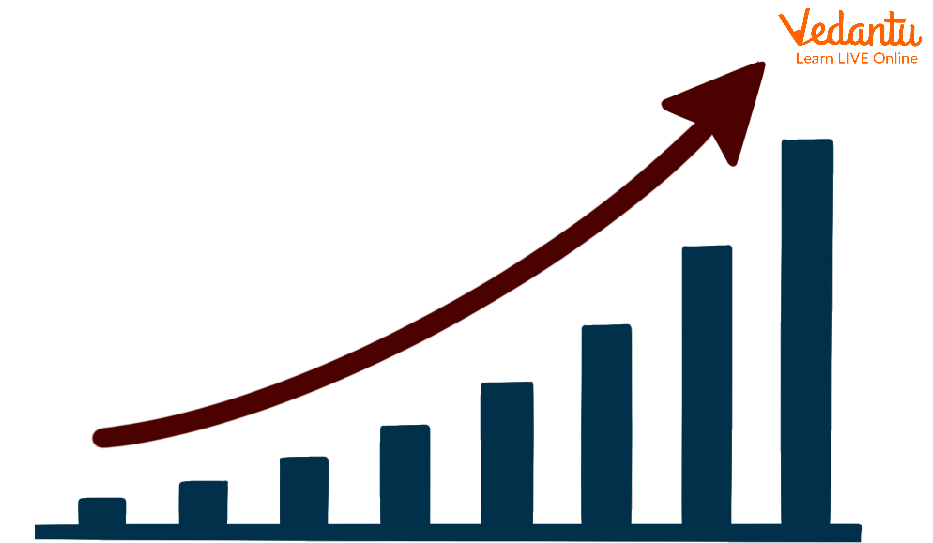
Benefits of Operation Costing
The following are just some additional benefits of learning about operation costing:
Restrain your Spending - Professionals might find savings by using operation costing to analyse where their money is spent in manufacturing. For instance, if the firm's accountants determine that too much money is being spent on rent for just a location that doesn't move much product, the corporation may choose to shut down that location and reallocate the stock elsewhere.
Control and Evaluate the Administration - A separate expert may oversee each manufacturing phase. By analysing these processes through operation costs, a business may determine where enhancements can be made, allowing relevant management to pursue more education and alter their methods accordingly.
Save Time and Effort - The results of a cost estimate for running operations may be used to pinpoint inefficient steps in a company's workflow. For an example of operating cost, if an accountant sees a lag in orders slowing down inventory delivery, they could recommend changing the ordering software.
Fidelity Improvement - A company's total budget will reflect the operating expenses it has calculated. This might aid in their cost accounting and resource management.
Assume that the Market will Constantly be Changing - Product, labour, and maintenance costs may shift due to economic fluctuations. Knowing how much things have cost in the past might help a business prepare for future changes.
Conclusion
The costing technique, which determines the unit price of the product from each operation and is a step in the manufacturing process, determines the price per unit. A critical distinction between activity-based costing and process costing is the emphasis placed on treating each activity as its cost centre. This means that we keep track of the total cost of all the stuff we use and the people we pay to do it for each process. At the same time, each function receives its fair share of overhead costs.
FAQs on Operation Costing: Definition and Examples
1. What is Operation Costing, and in which industries is it commonly used?
Operation Costing is a method of cost accounting used to determine the cost of providing services. Unlike methods used for manufacturing, it focuses on the expenses incurred in running a service operation. It is predominantly used in industries where the primary output is a service rather than a physical product.
Common industries include:
- Transport Services: Bus companies, railways, airlines, and goods transport agencies.
- Hospitality Services: Hotels, canteens, and restaurants.
- Utility Services: Electricity boards, water supply, and gas agencies.
- Entertainment: Cinemas, theatres, and amusement parks.
2. What are the main features of Operation Costing?
The primary features that distinguish Operation Costing from other costing methods are:
- Service-Oriented: Its main focus is on the cost of rendering services, not manufacturing goods.
- Composite Cost Units: It often uses a dual or composite cost unit for better measurement, such as 'passenger-kilometre' in transport or 'room-night' in hotels.
- Periodical Calculation: Costs are typically calculated for a specific period, like a month or a quarter.
- Classification of Costs: Costs are grouped into categories like Fixed (Standing) Charges, Semi-Variable (Maintenance) Charges, and Variable (Running) Charges for effective control.
3. How do you calculate the cost per unit in Operation Costing?
The cost per service unit is calculated by aggregating all operating costs for a period and dividing them by the total number of service units provided during that same period. The basic formula is:
Cost per Service Unit = Total Operating Costs for the Period / Total Number of Service Units
For instance, to find the cost per kilometre for a bus, you would sum up all costs (fuel, salary, depreciation, insurance, etc.) for a month and divide it by the total kilometres the bus ran in that month.
4. How are operating costs typically classified for calculation? Give an example.
For effective control and calculation, operating costs are generally classified into three main categories. For a transport company, this classification would look like this:
- Fixed or Standing Charges: These costs do not change with the distance covered, such as vehicle insurance, road tax, garage rent, and salaries of office staff.
- Semi-Variable or Maintenance Charges: These costs include expenses like tyre replacement, repairs, and vehicle servicing, which are partly fixed and partly variable.
- Variable or Running Charges: These costs vary directly with the distance or usage, such as the cost of fuel (diesel/petrol), engine oil, and wages of the driver and conductor if paid per trip.
5. What are the key objectives of applying Operation Costing in a service business?
The main objectives of using Operation Costing are:
- Cost Ascertainment: To accurately determine the cost of providing each unit of service (e.g., the cost per ride or per meal).
- Price Fixation: To set competitive and profitable prices, fares, or rates for the services offered.
- Cost Control: To monitor and manage expenses by comparing actual costs with standard or budgeted costs, helping to identify and eliminate inefficiencies.
- Informed Decision-Making: To provide management with reliable data for decisions like adding a new service route, purchasing new equipment, or discontinuing an unprofitable service.
6. How does Operation Costing differ from Process Costing?
Operation Costing and Process Costing are both methods of ascertaining costs, but they apply to different types of industries. The key difference is that Operation Costing is used for service industries where services are provided (e.g., transport, hotels), and the output can be non-uniform. In contrast, Process Costing is used in manufacturing industries where a product passes through a series of distinct, continuous processes to be completed (e.g., chemicals, textiles), and the output is homogeneous.
7. Why is the selection of a suitable cost unit so important in Operation Costing?
The selection of a suitable cost unit (like per passenger-km, per tonne-km, or per room-night) is crucial because it forms the basis for cost ascertainment and control. An appropriate cost unit ensures that costs are accurately allocated and that the calculated cost per unit is meaningful. An incorrect or poorly chosen cost unit can lead to misleading cost information, resulting in flawed pricing strategies, poor performance evaluation, and ineffective cost management for the service organisation.
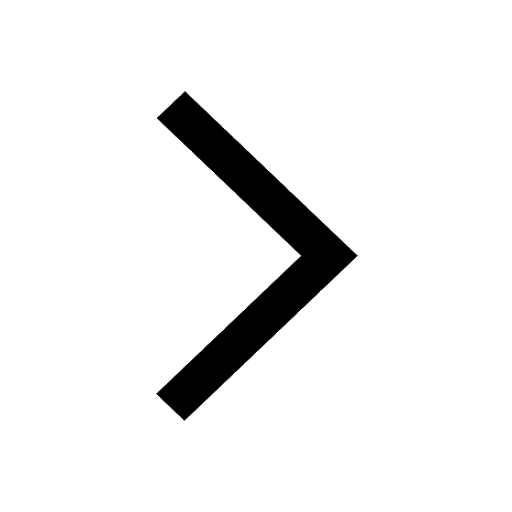
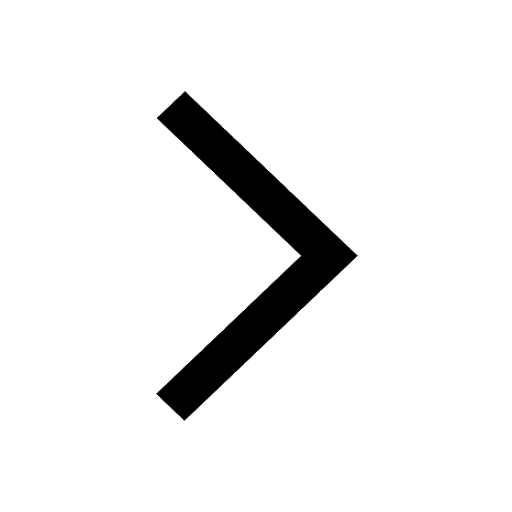
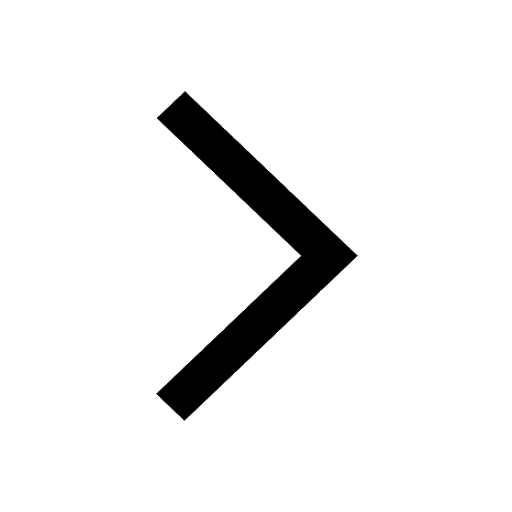
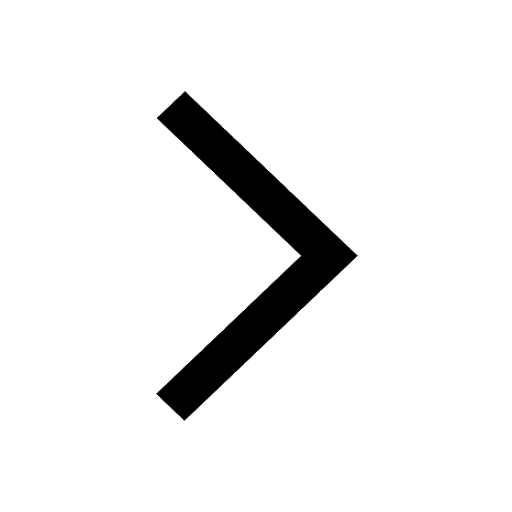
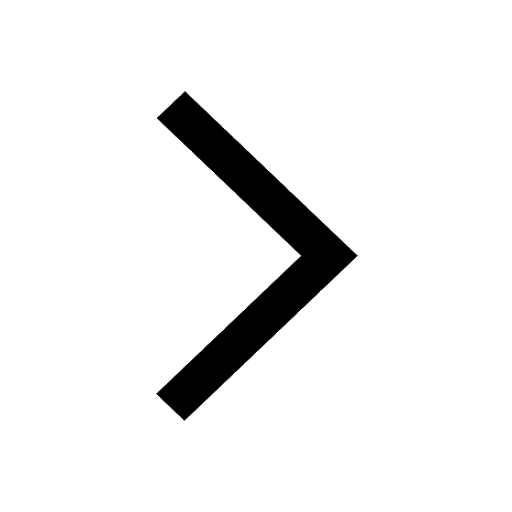
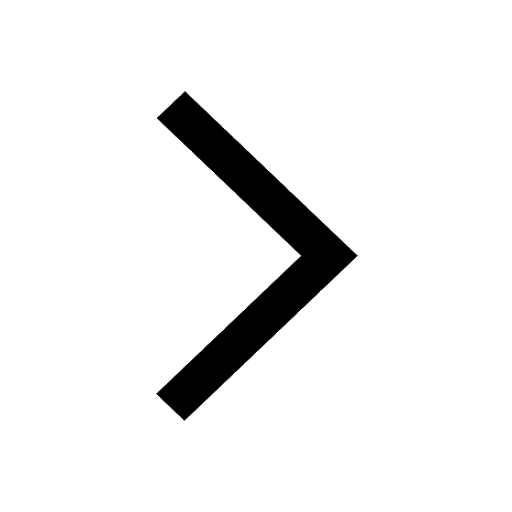