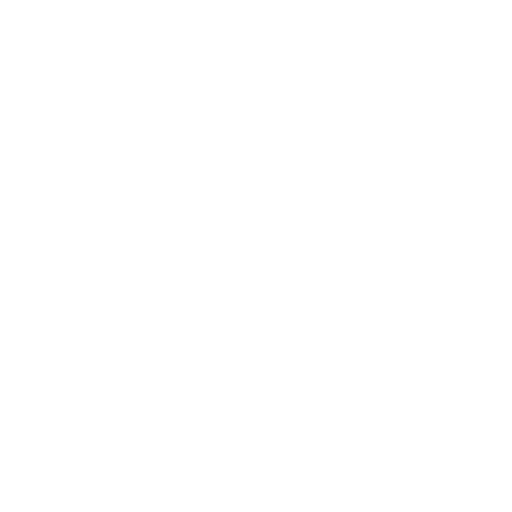

What Are the Main Steps in Metallurgical Processes?
Processes of Metallurgy is essential in chemistry and helps students understand various practical and theoretical applications related to extraction and purification of metals. It also shows how these metals are made available for real-life uses such as making wires, tools, vehicles, and more.
What is Processes of Metallurgy in Chemistry?
A metallurgical process refers to the methods used to obtain pure metals from their ores. This topic appears in chapters related to extraction of elements, mineral processing, and types of chemical reactions, making it a foundational part of your chemistry syllabus.
Metallurgy includes all steps from initial mining to final metal use and relates to both industrial and laboratory chemistry.
Steps of Metallurgy
The processes of metallurgy involve several key steps that convert naturally-occurring ores into pure metals. Here are the main metallurgical process steps:
- Crushing and Grinding of ore
- Concentration (Dressing) of ore
- Extraction of crude metal (Reduction)
- Purification or refining of the metal
- Alloying and shaping (in some cases)
Metallurgical Process Steps and Examples
Step | Description | Common Methods | Example |
---|---|---|---|
Concentration | Removal of unwanted impurities called gangue from ore | Gravity separation, Magnetic separation, Froth flotation, Leaching | Froth flotation for copper sulphide ores |
Extraction (Reduction) | Conversion of ore to crude metal by removing oxygen or other elements | Calcination, Roasting, Smelting, Electrolysis | Blast furnace for iron, Electrolysis for aluminium |
Purification | Removing remaining impurities from crude metal | Electrolytic refining, Zone refining, Distillation | Electrolytic refining of copper |
Why is Ore Concentration Needed?
Raw ores contain sand, clay, and other impurities that make them difficult or costly to process. Concentrating or "dressing" the ore increases the percentage of the target metal. This step uses physical and chemical separation methods:
- Gravity separation (Hydraulic washing): Used when ore particles are heavier than impurities, such as tin and iron ores.
- Magnetic separation: Ideal for ores containing magnetic substances like magnetite.
- Froth flotation: Mainly used for sulphide ores (like copper pyrites).
- Leaching: Chemical method where ore dissolves in a reagent, leaving impurities behind (e.g., bauxite leaching with NaOH).
Extraction and Reduction in Metallurgy
Extraction means obtaining crude metal from the concentrated ore, usually by reduction. This step depends on the chemical nature of the ore:
- Calcination: Heating the ore in the absence of air (removes water, decomposes carbonates). Example: ZnCO₃ → ZnO + CO₂
- Roasting: Heating the ore in excess air (converts sulphides to oxides). Example: 2ZnS + 3O₂ → 2ZnO + 2SO₂
- Reduction: Chemical process using carbon, CO, or by electrolysis (Al³⁺ + 3e⁻ → Al)
Refining or Purification of Metals
After reduction, crude metals often contain impurities. Refining gives metals fit for industry. Popular methods include:
- Electrolytic refining: Used for copper, silver, aluminium
- Zone refining: For silicon and germanium (semiconductors)
- Distillation and liquation: For metals with low/high melting points
Types of Metallurgy
There are different branches of metallurgy:
Type | Description | Example |
---|---|---|
Extractive Metallurgy | Covers extraction of metals from ores | Iron extraction from haematite |
Physical Metallurgy | Studies structure and properties of metals | Heat treatment of steel |
Process Metallurgy | Applies process engineering to metals | Continuous casting |
Step-by-Step Reaction Example: Extraction of Aluminium from Bauxite
1. Concentrate bauxite ore using leaching with NaOH.2. Separate insoluble impurities by filtration.
3. Precipitate aluminium hydroxide by passing CO₂.
4. Heat to get pure Al₂O₃.
5. Use electrolysis (Hall–Heroult process) to reduce Al₂O₃ to aluminium metal.
Lab or Experimental Tips
Remember, gangue is always an impurity in ores, and flux is added to form slag. In Vedantu sessions, tricks like “calcination for carbonate, roasting for sulphide” help students recall the right process quickly.
Uses of Processes of Metallurgy in Real Life
Metallurgy makes all metals in our life possible—from kitchen utensils and vehicles to electrical wires and even modern electronic chips. Pure and alloyed metals created via these processes build bridges, machines, and more.
Relation with Other Chemistry Concepts
Processes of metallurgy connect with redox reactions, types of chemical reactions, and methods of separation. They also relate to principles of thermodynamics in chemistry and environmental science due to their impact on pollution and recycling.
Final Wrap-Up
We explored processes of metallurgy—from ore dressing and extraction to refining and real-world applications. Clear understanding of each step makes metallurgy easier and exam-ready. For more explanations and live guidance, check Vedantu’s chemistry resources.
FAQs on Processes of Metallurgy: Extraction and Purification of Metals
1. What are the main steps in the processes of metallurgy?
The main steps in metallurgy are:
• Concentration of ore (removal of impurities)
• Extraction of metal (reduction of ore to crude metal)
• Refining (purification of metal)
• Alloying and shaping (for industrial application)
Each step is essential to obtain pure, usable metals from their natural mineral sources.
2. What is the importance of the concentration of ore in metallurgy?
Concentration of ore separates valuable metal compounds from unwanted gangue (impurities).
This step:
• Increases metal yield
• Reduces energy and reagent costs in later stages
• Enables more efficient extraction and purification processes
3. What is the difference between calcination and roasting?
Calcination and roasting are thermal processes used in metallurgy:
• Calcination: Heating ore in limited or no oxygen (removes moisture, decomposes carbonates)
• Roasting: Heating ore in excess oxygen (converts sulfides to oxides)
Calcination is for carbonate ores; roasting is for sulfide ores.
4. How is aluminium extracted from bauxite ore?
Aluminium extraction from bauxite involves:
1. Purification of bauxite using Bayer’s process
2. Electrolytic reduction of alumina (Al2O3) in molten cryolite
3. Refining aluminium using electrolytic methods
This produces pure aluminium metal for use in industries.
5. What methods are used for refining metals during metallurgy?
Metal refining methods include:
• Electrolytic refining (for copper, aluminium, etc.)
• Distillation (for low-boiling-point metals like zinc and mercury)
• Poling (using green wood poles for copper)
• Liquation (for low melting metals such as tin)
Efficient refining ensures high-purity metals.
6. What is the role of a blast furnace in iron extraction?
A blast furnace is used in the extraction of iron from its ore (haematite).
It achieves:
• Reduction of iron oxides by carbon monoxide
• Separation of molten iron and slag
• Continuous production of pig iron for steel making
7. How are environmental concerns addressed in metallurgy?
Modern metallurgy addresses environmental concerns by:
• Using pollution control technologies (filters, scrubbers)
• Recycling metals and process by-products
• Reducing energy use with more efficient methods
• Managing waste safely and reusing slag wherever possible
8. What is the difference between physical and chemical processes in metallurgy?
Physical processes in metallurgy involve physical separation of ore from impurities (e.g., gravity separation, froth flotation).
Chemical processes involve conversion of compounds using reactions (e.g., calcination, roasting, reduction).
Both types are used at different steps for efficient metal extraction.
9. What is hydrometallurgy, and how does it differ from pyrometallurgy?
Hydrometallurgy extracts metals using aqueous solutions (e.g., leaching of gold with cyanide).
Pyrometallurgy involves high-temperature processes (e.g., smelting of iron).
Hydrometallurgy is suitable for metals soluble in water; pyrometallurgy is used for metals stable at high temperatures.
10. Why are some metals, such as gold and platinum, found in a native state?
Gold and platinum are found in native state because:
• They are chemically unreactive
• Do not combine easily with other elements
• Remain unchanged in earth’s crust over time
This allows easy recovery by simple physical methods.
11. Can you provide examples of concentration methods used in metallurgy?
Common ore concentration methods include:
• Gravity separation (based on density difference)
• Froth flotation (for sulfide ores using foaming agents)
• Magnetic separation (for ores with magnetic properties such as magnetite)
Selection depends on the type of ore and impurity present.
12. What factors determine the choice of extraction method in metallurgy?
Choice of extraction method depends on:
• Nature of ore (oxide, sulfide, carbonate)
• Metal reactivity (reactivity series)
• Economic and environmental factors
• Purity required for end use
Different metals need different extraction and purification approaches based on these factors.
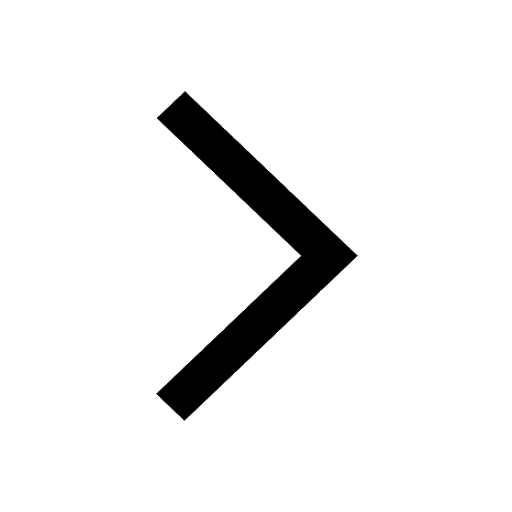
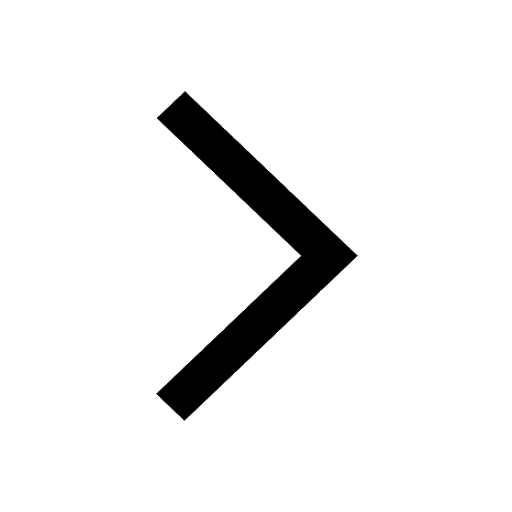
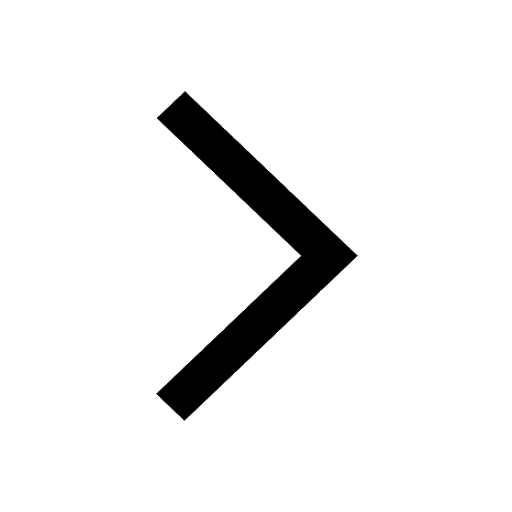
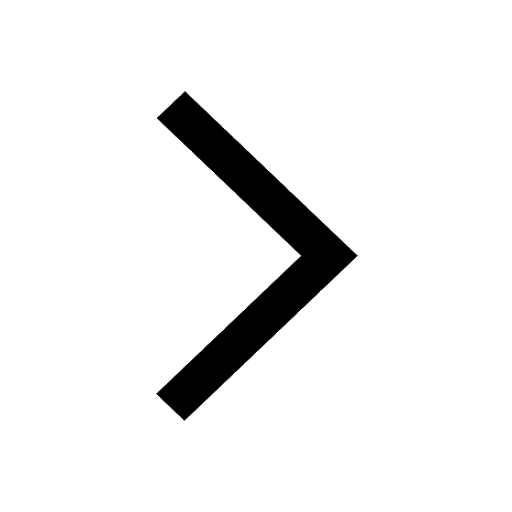
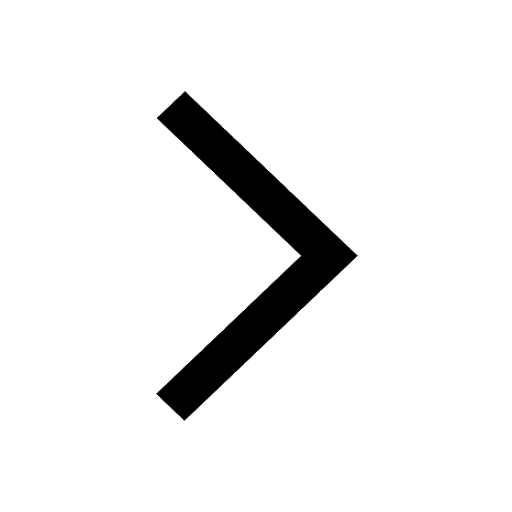
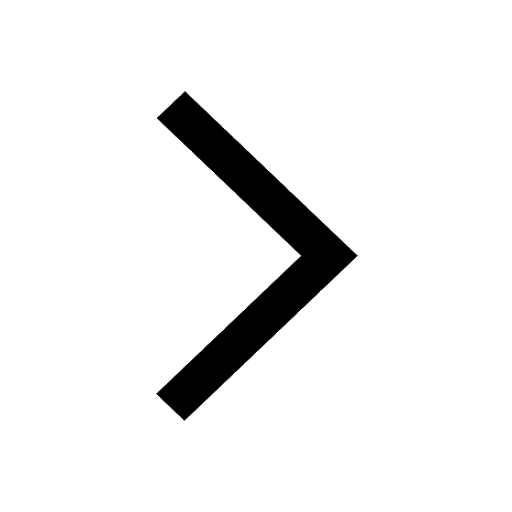